A metal lathe is a mesmerizing machine. Watch it spinning a workpiece at high speed. Then the metal gets smaller and smoother—almost like magic. Except it isn’t magic at all.
Nothing happens on a metal lathe without skill and attention. At least, nothing good. If you don’t follow the fundamentals of effective lathe operation, you’re likely to end up frustrated, injured, or just plain dead.
Fortunately, we’re here to equip you with these helpful tips to make your metal lathe work easier and safer.
Know How to Dress Like a Machinist and Why We Dress How We Do
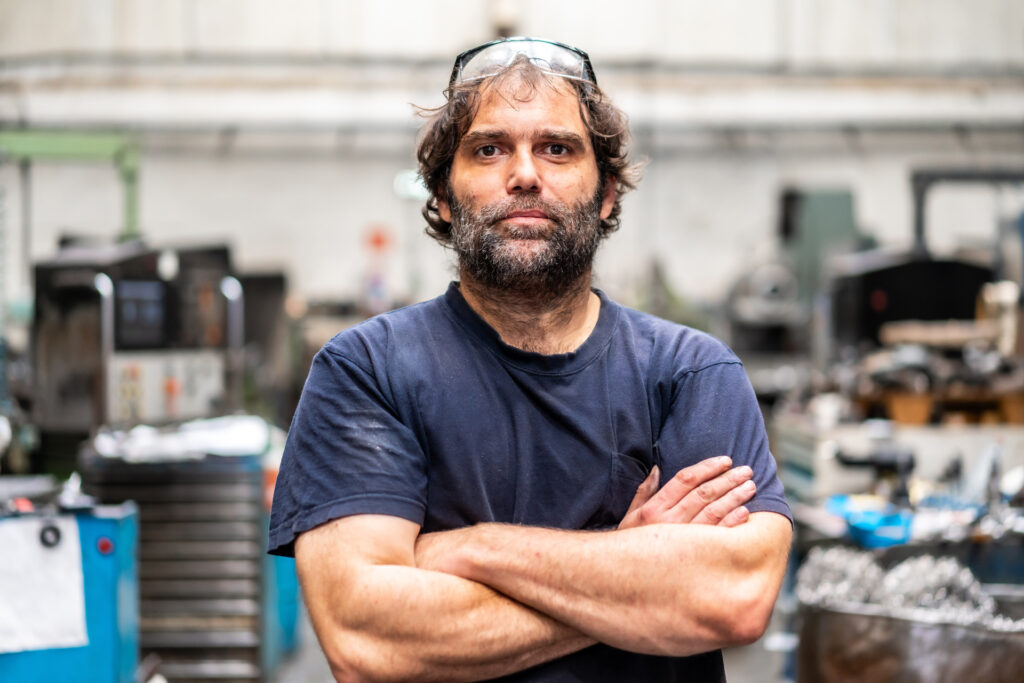
If you want to express your loose, laid-back style, do it outside the shop. Because anytime you’re around a metal lathe, loose clothes are a no-go.
In fact, anything baggy or hanging at all is off-limits for a machinist. Some of this is fairly obvious, like hanging jewelry that can easily get caught in the machine.
But other out-of-bounds attire might surprise you. Long sleeves, for example. These can also get caught. Or rings, which can snag and cause an ugly finger injury called degloving.
Here’s the machinist’s uniform to stick to:
- Short-sleeved shirt tucked in
- Snug-fitting work pants or jeans
- If you wear a watch, only one with a metal band
- Steel-toed boots
And if you have a belt, a common practice is to feed the end back under one loop to the left so it’s facing away from the machine.
If the Chuck Key Is in the Chuck, Your Hand Is on It. End of Story.
The chuck key tightens or loosens the jaws of the chuck to secure your workpiece in place.
Leaving the chuck key in the chuck and then starting the machine can cause catastrophic consequences. The key can suddenly become a high-speed metal projectile.
By keeping your hand on the key, you will remember to remove it from the chuck immediately after making adjustments. It’s a simple thing, but it can save lives.
Don’t Touch Anything That Moves With Gloves On
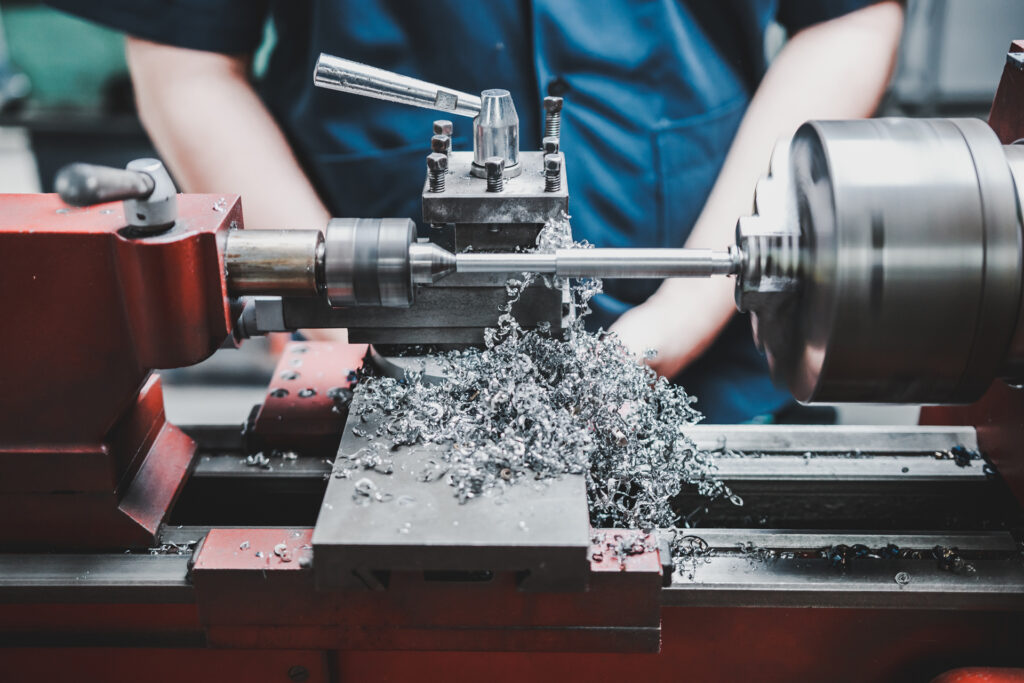
There are some shop activities in which you benefit from wearing gloves to protect your hands. Working anywhere near powerful rotating machinery, including lathes, is not one of them.
Keep gloves of any kind off when working with a lathe. The material can get caught, and you’ll never win that battle.
Just Assume Everything is Hot or Sharp
Interesting thing about metal. You’ve probably observed it before. Metal is a great conductor of heat.
Parts coming off a lathe are hot. So are lots of others. But the good thing is, they also cool off relatively quickly, so just give it a minute to cool off. That 5 minutes isn’t worth getting a nasty burn.
Lots of workpieces and metal parts around your shop will also have sharp edges.
Therefore, just proceed with caution with any piece of metal.
Put a Radius or a Chamfer on Everything. There’s No Reason Not to.
A radius or fillet is a rounded corner. A chamfer is a flattened or beveled one. They’re both ways of getting rid of sharp edges.
Adding these features not only makes metal parts less likely to injure. They also make them better looking. They’re always good skill practice, too.
So, all around, a win-win-win.
Learn Your Machine and Its Quirks
Know how to use your metal lathe safely. Always follow safe operating practices.
That might seem pretty obvious. But every machine is different. An old model of a lathe is going to perform differently from one that’s brand new.
It’s not just a matter of condition. It might also have different accessories, fixtures, etc. And, of course, tooling comes with all kinds of variability.
Your machine might require some scrap passes just to get warmed up. There might be a spot on an axis where it’s not quite accurate.
Learning these quirks takes time and patience. Ultimately, this intimate expertise will pay off and bring better results.
Use Sharp Tools
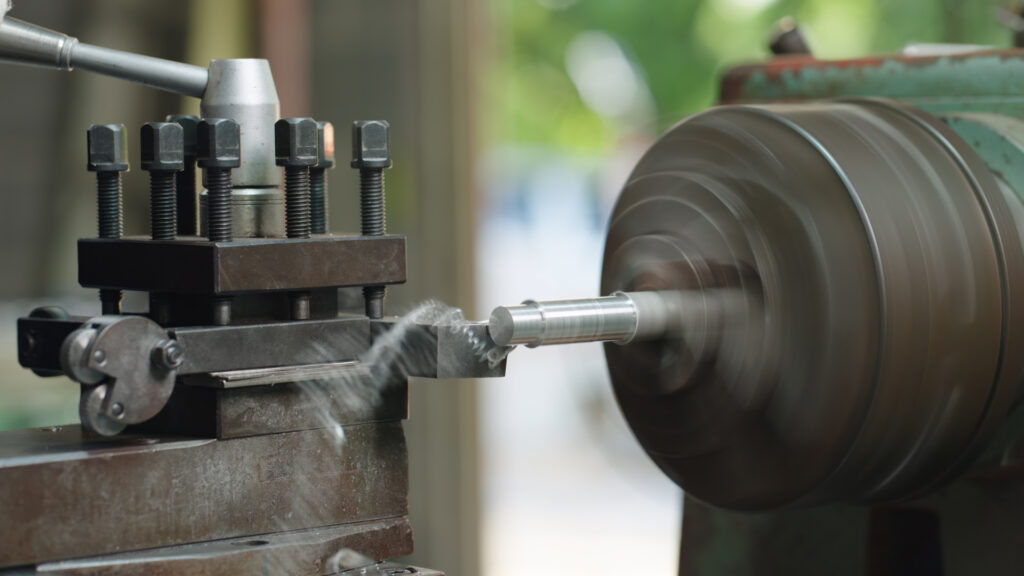
You might be tempted to buy cheap tools. The price differences can be stunning. Or you might be tempted to try to stretch the life of the tool out a little too long.
But high-quality, sharp tools make all the difference in the world. Cheap or old tooling breaks. When it does, other stuff breaks, too. The amount of scrap you create with cheap tools or trying to stretch your tool’s life gets costly quickly. Not to mention your costs in terms of added time and frustration.
Opt for quality tooling whenever possible and change your tooling when it gets dull.
Skim Your Jaws
When you’re using soft jaws—made of mild steel or aluminum—skimming helps make sure you have maximum surface contact with the workpiece.
Basically, skimming involves machining just a bit of material from the surface of the jaws.
It helps minimize slippage, so it’s a smart way to ensure precise and consistent results. Oh, and it makes the workpiece less likely to fly across the shop, becoming a deadly projectile.
Know How to Talk Like a Machinist
You’ll hear lots of colorful language around a machine shop. Some of it’s useful; some of it’s not. Very little of it will make sense to the uninitiated.
But instead of getting confused or possibly offended, it’s best to pick up as much of the slang and lingo as quickly as you can.
You may already know some of the important ones, like “thou” for a thousandth of an inch. Or a “tenth” to mean 0.0001 or a tenth of a thousandth inch. Tricky!
Every machinist has favorites, like “hogging” for using high speeds and feeds … “gravy” for an easy job … “button monkey” for a CNC operator …
You’re sure to have your own go-tos once you learn a few.
Measure Twice, Cut Six Times
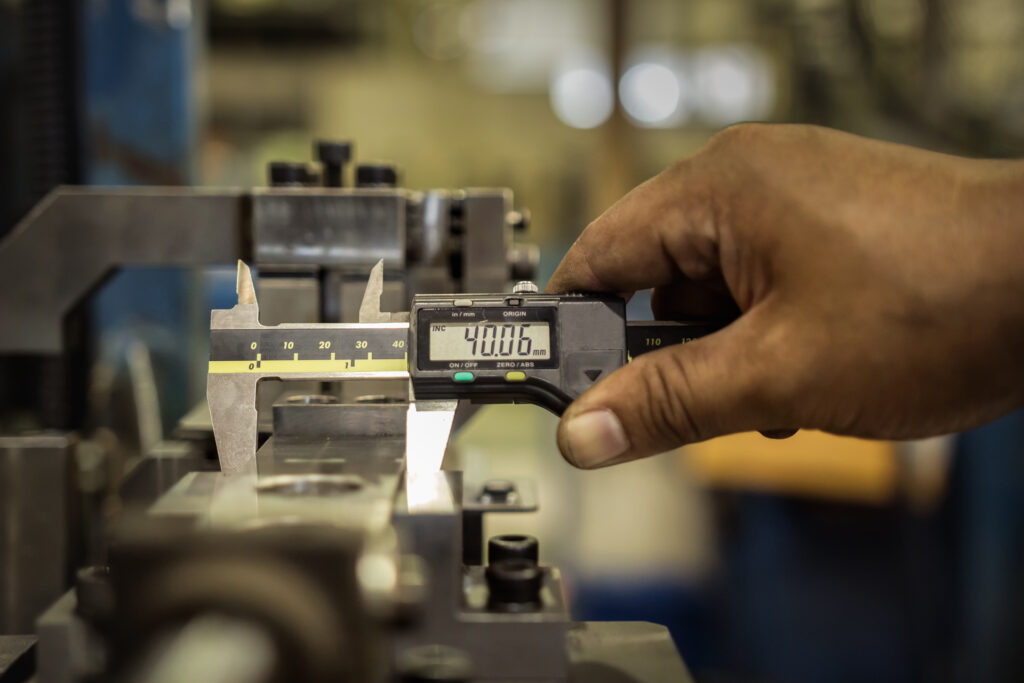
This is the old carpenter’s proverb adapted for machinists.
The idea is that you need to pay attention to details when planning your cuts. Then,d you need to be methodical and patient when doing the actual cutting.
Going too deep with one pass can put too much stress on your tool and your machine. You might break the tool or end up with scrap.
Take your time with multiple passes instead.
Feeds and Speeds – Need I Say More
It’s the dynamic duo of machining success. These two parameters will go a long way to determining accurate and efficient results.
Feed is the rate at which the cutting tool advances along your workpiece; speed is the rotational speed of the spindle. Feeds and speeds that are too low lead to inefficiency and heat buildup. Those that are too high can lead to tool breakage or poor surface finish.
Depending on the metal, tool, part geometry, and other factors, there’s always a balance where the cutting tool can remove material at an optimal rate. Mastering this balance is the single biggest advantage of a skilled machinist.
Fortunately, you can find an array of helpful speed and feed calculators online. You can always experiment a bit with different settings—another great way to advance your skills and expertise.
Always Use 3-Phase Power
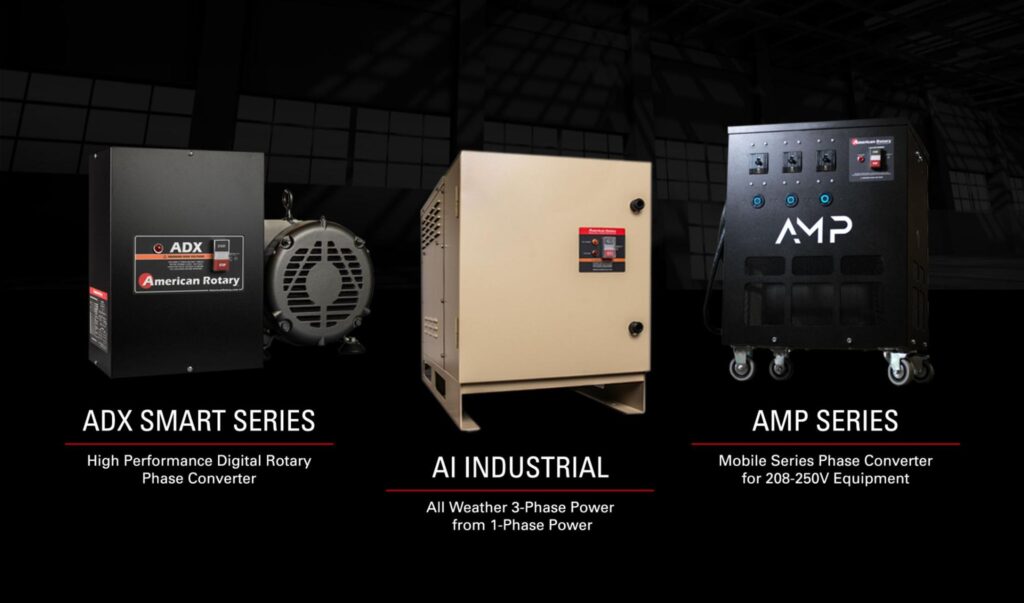
Higher horsepower really comes in handy when cutting metal. A good metal lathe in a pro shop may have a motor with 3+ horsepower.
At that level, 3-phase electricity (vs. standard single-phase service) enables smoother operation and higher torque—leading to more efficient cutting, better surface finish, longer tooling life, and less scrap.
So, how do you power a 3-phase metal lathe? Using a rotary three-phase converter is a great solution.
USA-made American Rotary phase converters easily convert your single-phase to reliable, efficient 3-phase power. With proper sizing, you can power a three-phase lathe along with other machines and devices—both 3-phase and single-phase—at the same time.
It’ll keep your lathe and the shop running while you build your skills. Check out our full product line and contact us with questions.