CNC machining is great for a lot of different applications. But you need a stable and consistent power supply, or you risk damaging this valuable equipment. Is a rotary phase converter a good option for powering CNC machines? Yes, but you’ll need to keep some key considerations in mind.
First off, why would you need a rotary phase converter for CNC machining?
If you have a shop in a residential or rural area, you probably have single-phase electric utility service, the common residential and light-commercial variety. If you have three-phase CNC machining equipment—which you may want for higher workloads and greater efficiency—you’ll need to find a way to power it.
Getting three-phase power installed by your utility can be cost-prohibitive. That’s where a phase converter comes in, converting your single-phase electricity to three-phase power for CNC machining and other equipment.
In this article, we’ll explore what you need to know when choosing a rotary phase converter for CNC machining in your shop.
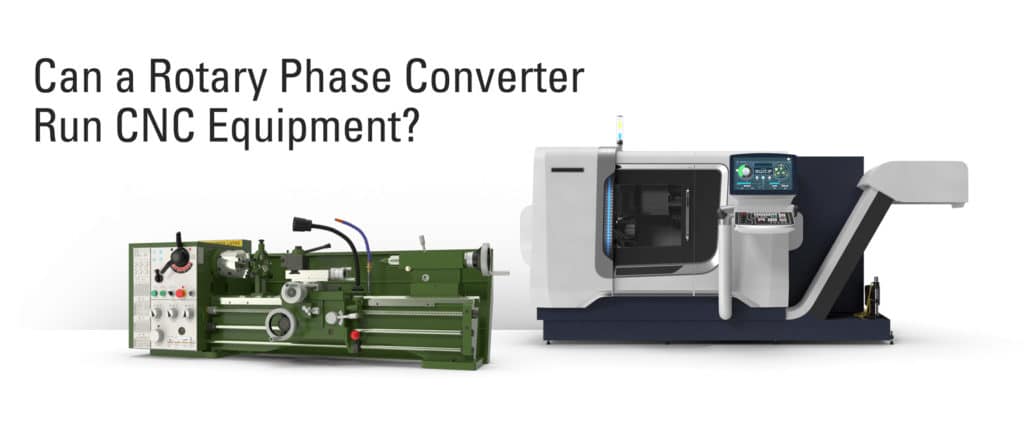
Can a Rotary Phase Converter Run CNC Equipment?
Yes, a rotary phase converter can run your CNC equipment. But not just any rotary phase converter can do the job.
Whether you need to drill, mill, or carve out a nearly limitless range of plastic, metal, and wood materials, CNC (computer numerical control) machining will help you do it quickly, consistently, and at high quality.
However, the precise output of CNC machining must begin with precise inputs: In other words, you’ll need a precise power supply.
Among all the equipment you might be running in your shop, CNC machines are bound to be among the most voltage-sensitive. That means that you need a consistent and stable power supply without wide swings in the voltage.
Generally speaking, three-phase CNC machines require a voltage balance of +/- 5% or better. In other words, the difference in voltage among the three phases should be less than 5%. Going outside this range can dramatically reduce the performance and lifespan of your motor.
Only certain makes and models of rotary phase converters, such as American Rotary’s AD series digital rotary phase converter, can meet these voltage balance requirements. You’ll need to make sure that the rotary phase converter you choose will deliver.
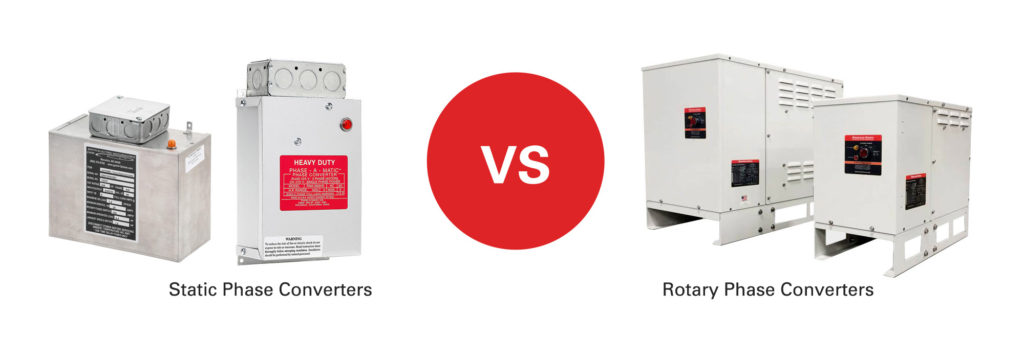
Static Phase Converters vs. Rotary Phase Converters for CNC Equipment
The two main types of phase converters, static and rotary phase converters, both turn standard single-phase electricity into three-phase power. But if you’re wondering about static phase converters for your CNC machining systems, you’ll need to go with a different option.
Static phase converters can start 3-phase motors but should not be used to operate a CNC machine. The reason is that, once an electric motor has been started, the static phase converter will disengage and allow the electric motor to run only on single-phase power.
The resulting power is unbalanced, and the equipment can only operate up to around two-thirds of its rated horsepower before forcing too much current through the winding of the motor.
This unbalanced output and the resulting “single-phasing” of a 3-phase motor is hard on 3-phase equipment and may shorten the life of the motor itself.
You might also consider a third type, a more complex solid-state phase converter, which can provide a voltage balance of 1% or better. The issues there include cost, limited warranty, and difficult or expensive repairs due to the internal complexity, which includes hundreds of components.
A rotary phase converter, meanwhile, is highly reliable and can create continuous, well-balanced three-phase power.
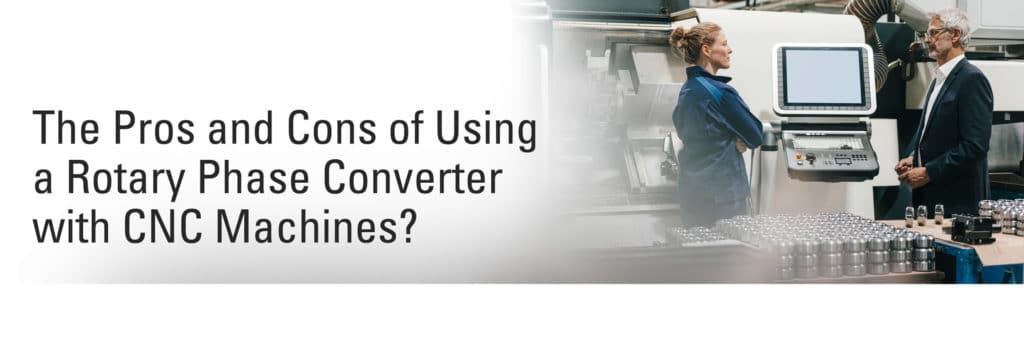
The Pros and Cons of Using a Rotary Phase Converter with CNC Machines?
As we said before, not all rotary phase converters should be trusted with your CNC machining equipment.
To supply the precise voltage balance that protects your equipment, you’ll want a rotary phase converter that is digitally controlled.
American Rotary provides a number of digital rotary phase converters, all of which use our patented MicroSmart Controller, which monitors voltage every millisecond to help provide precise voltage balance at 1-5%, well within the proper range for CNC equipment.
Can You Run Other Types of Equipment at the Same Time?
The good news is that, with proper sizing, you can run an entire shop off a single rotary phase converter. Many rotary phase converters can accommodate very small, lightly loaded machines and very large or heavily loaded machines.
Voltage-sensitive equipment such as CNC and more general-duty equipment—including both resistive/motor and non-motor/inductive loads—can be run off a rotary phase converter.
What is the Lifespan of a Rotary Phase Converter?
Most rotary phase converters are reliable and low-maintenance pieces of equipment. You may occasionally need to add some bearing grease.
Many American Rotary phase converters have been in use in shops across the country for decades. Our machines are backed by a lifetime warranty, too.
Other Considerations for Using and Maintaining a Phase Converter
Some people worry about the potential noise of a rotary phase converter in their shop. It’s true that some models can be noisy.
But American Rotary’s variable impedance technology, which is the key to reliable system startups, also makes noise much less of an issue.
The custom-designed VIT generator runs much smoother and quieter than a typical three-phase motor. The idler will operate at less than 60 Db, which is comparable to a box fan running. In most cases, your three-phase machine will drown out the sound of the phase converter.
If you still have noise concerns or severe space constraints, you can get an outdoor-rated phase converter with a 3R enclosure, such as the American Rotary AI industrial-grade rotary phase converters.
Some Examples of CNC Equipment You Can Run with a Rotary Phase Converter
CNC machines are valuable in a vast array of industries, from general manufacturing, electronics, and consumer products to medical, aerospace, defense, and more.
With a right-sized rotary phase converter in your shop, you’ll have no problem running CNC equipment such as:d
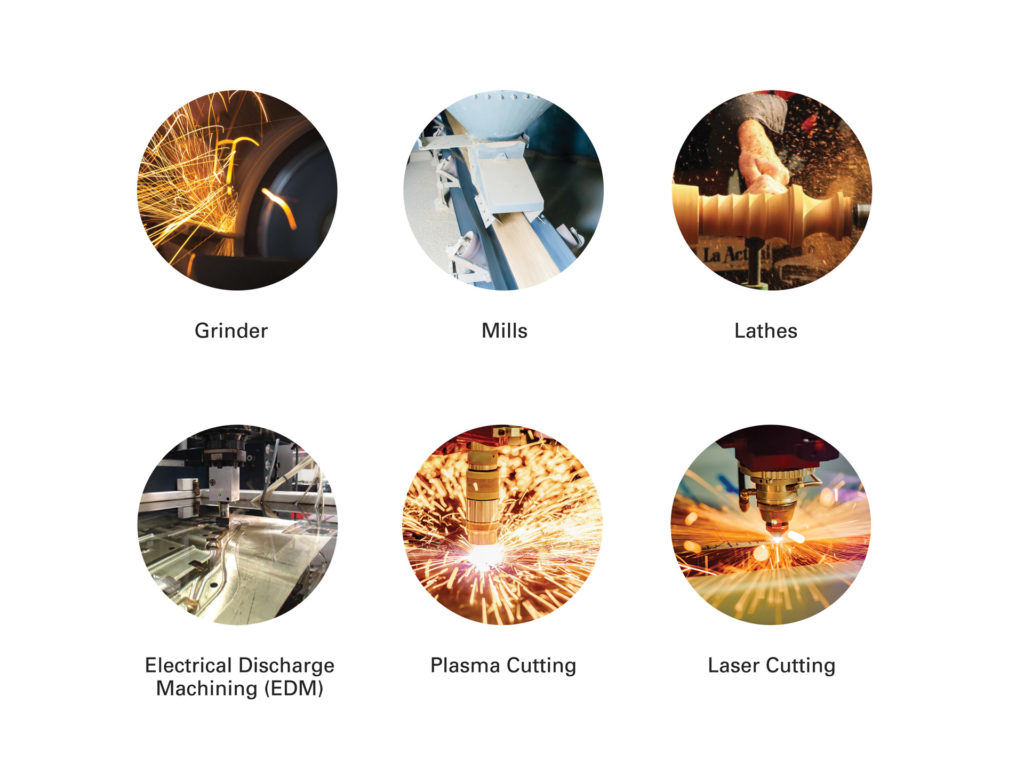
- Mills
- Lathes
- Electrical discharge machining (EDM)
- Plasma cutting
- Laser cutting
- Grinders
And you can run it all with a rotary phase converter!
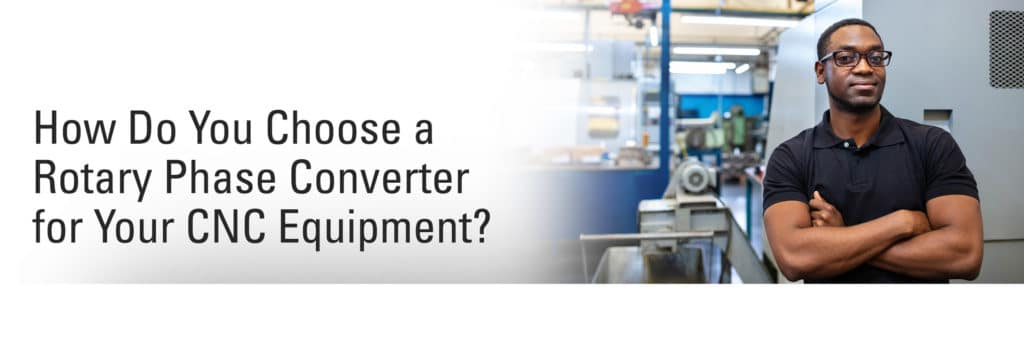
How Do You Choose a Rotary Phase Converter for Your CNC Equipment?
The biggest issue to start is how much power you need for your equipment. Selection criteria include the horsepower, amps, kilowatts, and voltage of your machines.
Different types of equipment loads call for different kinds of converters. For example, the American Rotary ADX Extreme Duty Smart Series rotary phase converter is designed for high inertia/friction loads. The ADX rotary phase converters have current control to provide consistent torque while starting high inertia, extremely hard starting loads, yet are precise enough for CNC applications.
In any case, make sure the rotary phase converter you choose is rated for the specific kilowatts that your CNC equipment requires. You may want to go with a larger load than you currently require to leave room for future needs.
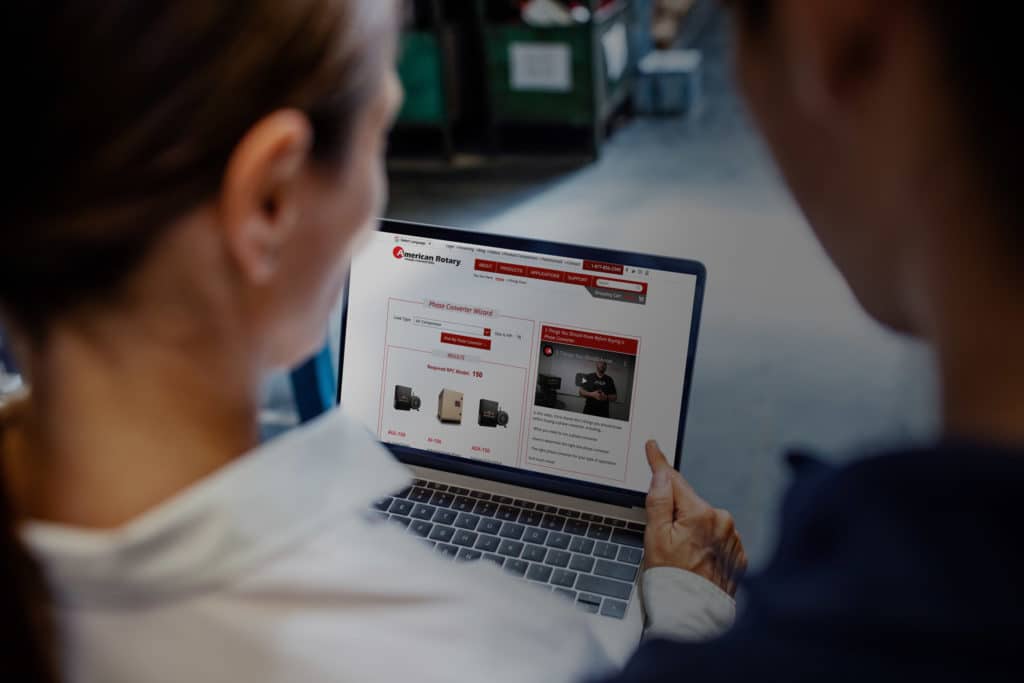
To get started in your selection, you can try American Rotary’s phase converter sizing wizard tool here.
Or feel free to call us at 888-743-6832, and our experts would be happy to help!