Considering doing some welding in your shop? Great idea! Welding is one of the primary forms of metal fabrication. As a hobbyist, you have four main choices for welders: flux-core arc, gas metal arc (or MIG), gas tungsten arc (or TIG), and stick. There are several other specialized welding processes, as well. But in this article, we’ll stick to the fundamentals.
Is there anything cooler than welding? Fusing two metal parts together by applying heat, pressure, and filler material is a sight to behold. DIY enthusiasts find it useful in many ways.
The welding process is fascinating and can be fun, too, but welding is a skill with a learning curve. A good place to begin is by understanding the different types of welding processes. While there are more than 30 different types of welding processes – including plasma arc welding, atomic hydrogen welding, and electron-beam welding – the 4 main types are Flux Core, MIG, TIG, and Stick. So let’s take a look at each of these 4 types.
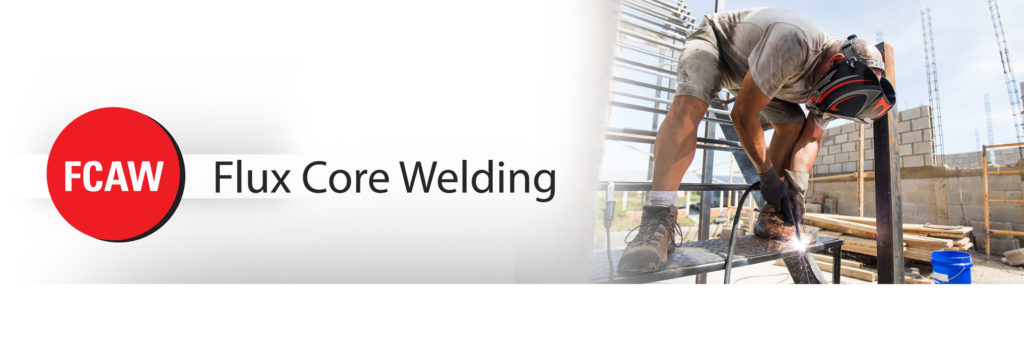
Flux Core (FCAW)
Flux-cored arc welding offers a combination of portability, speed, and affordability. It’s ideal for doing general repairs, working with rusty material, fabricating at construction sites, or welding outdoors in the wind.
FCAW is similar to the next type of welder we’ll discuss, but with one key difference: it doesn’t need a shielding gas. Other welding processes need gas that protects the weldment from contamination. In the FCAW process, the machine feeds an electrode filled with “flux” – a material that protects the arc. That’s why it’s more portable and better to use outside.
The main drawbacks to an FCAW welder are that they cause a lot of spatter, and most dedicated FCAW machines don’t draw a lot of power, so they can’t be used to weld thicker metals. Other drawbacks are that they can’t be used to weld many common alloys and that they produce heavy fumes, so you’ll need a well-ventilated area.
But flux core works on all the most common welding metals (carbon steel, stainless steel, and aluminum). And you can use it in any basic welding position (flat, horizontal, vertical, or overhead) or even out of position. Those perks and the machines’ affordability make an FCAW machine one of the best welders for a hobbyist.
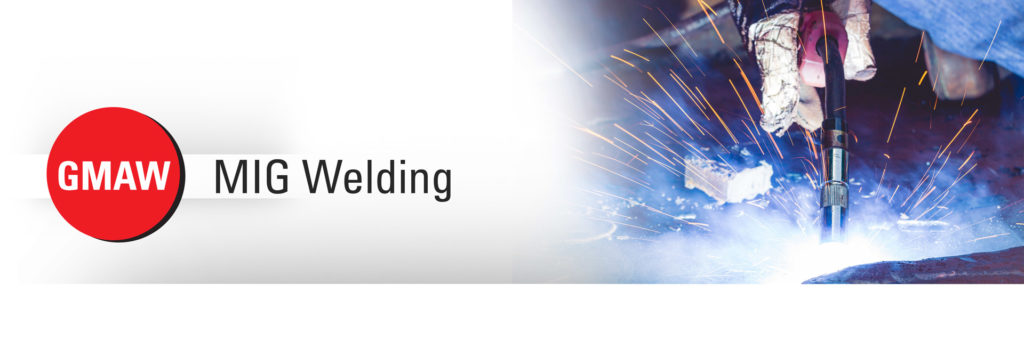
MIG (GMAW)
Gas metal arc welding, also called metal inert gas (MIG) welding, is a high-speed process that’s fairly easy to learn. This and the fact that you can make clean and strong welds is why it is the most common type of welding used in manufacturing.
Unlike flux core, you can use it with 26 gauge or thicker metals. But if you need to work with specialty metals such as copper, brass, titanium, etc., you’ll need to look elsewhere.
As the name suggests, MIG welding differs from flux core in needing shielding gas, typically argon or helium, to protect and shield the weld, preventing porosity. But otherwise, you can MIG weld with the same equipment used for FCAW.
MIG welders are wire feed machines, meaning they feed your filler metal at a consistent speed from a roll of MIG wire. Electricity melts the wire and the weld joint of the parent material together, creating a strong and great-looking weld.
Unlike flux core, MIG takes less cleanup. But the need for an external gas supply makes it less portable. So many hobbyists prefer the flux core approach for versatility.
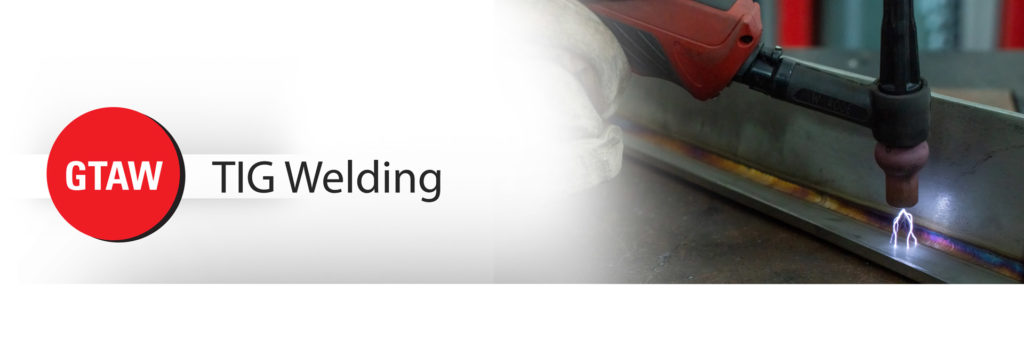
TIG (GTAW)
Gas tungsten arc welding, also called TIG (or tungsten inert gas) welding, enables high-precision, aesthetic welds.
But here are two key caveats: TIG welding is tougher to learn and slower to perform. It’s excellent for great-looking weldments of thin pieces of stainless steel, magnesium, copper, and more – if you know what you’re doing.
In GTAW/TIG, a consumable tungsten electrode shot through with variable current, controlled by a foot pedal, produces the weld. Unlike flux core and MIG, you’re holding a consumable filler rod in one hand with your torch in the other, instead of a continuous wire feed, where you have your feeding hand holding your gun and a bracing hand.
What’s more precise about TIG? You can control the amount of current and, therefore, the heat with a foot pedal. As a result, you can create durable, high-quality welds.
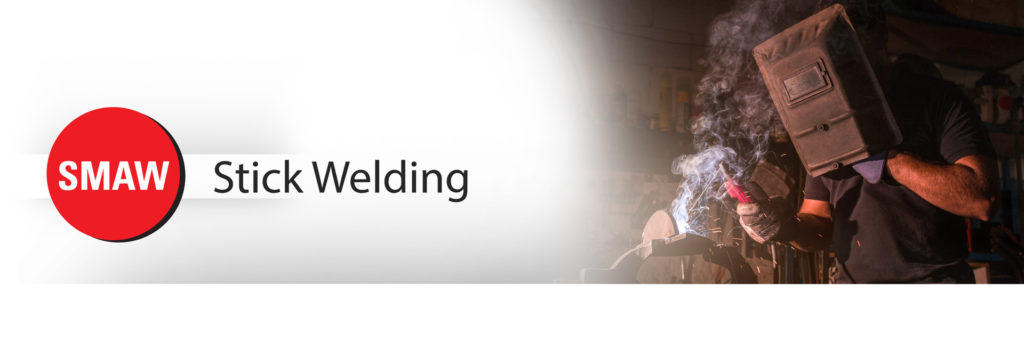
Stick (SMAW)
Stick welding, also called shielded metal arc welding (SMAW), is a well-known workhorse. It involves current flowing through an electrode rod to the parent material.
Compared with TIG welding, stick welding is generally the easiest to pick up and requires the least amount of experience. You can produce a strong weld with very little experience with a stick welder, even on rusty materials. And like flux-core, stick welding is well-suited for outdoor use since it doesn’t require a shielding gas.
Stick welding is the inverse of flux core welding in that it is almost always used for thicker metals (18+ gauge). However, almost all of the other downsides are the same. You’ll be limited to the metals you can weld, there is a lot of spatter, and stick welding produces heavy smoke, so it requires a well-ventilated area to work in.
Still, given its simplicity and accessibility, SMAW remains popular for everyday maintenance around the house, the farm, and other basic metal handiwork.
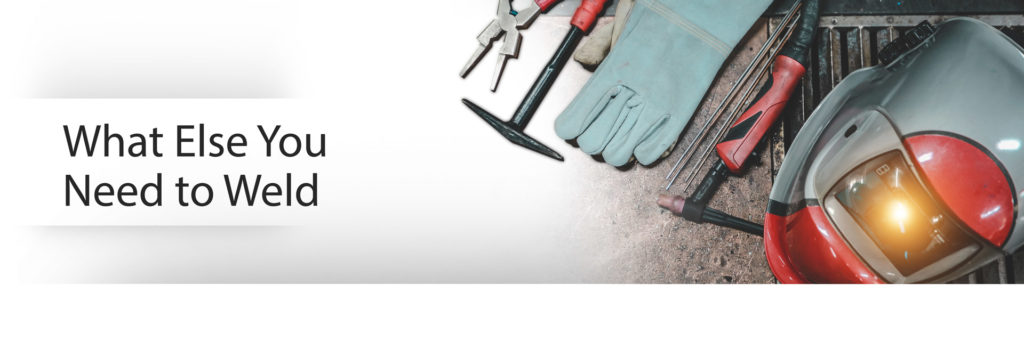
What Else You Need to Weld
The choice of welding machine is the biggest factor in getting started. But it’s not the only legwork. Among the other things you need to address:
- Personal protective equipment (PPE) – A cool-looking welding helmet to guard your head against hot metal and your eyes from intense light, plus insulated gloves and flame-resistant clothes or an apron.
- Welding clamps or magnets – For stable setup of your workpieces.
- Your workspace – Consider a welding workbench and make sure you have plenty of room.
- Hand tools – Welding pliers, metal brush, chipping hammer, speed square, and sheet metal gauge are among those that come in handy.
- Cleanup equipment – If you want to use a flux-core or stick machine, consider a welding fume extractor or a shop fan to help everyone breathe easy.
- Other metalworking tools – Check out our other blog post for more info.
Just as important is your power supply. By their very nature, Welders are electricity-intensive machines, with only some small FCAW machines being able to plug into a regular 110-volt outlet. The most robust and reliable among them may take three-phase power vs. the single-phase electricity that serves most residential areas.
The good news is that you can power your welder with that service. In fact, if you have the amps available, a good rotary phase converter will run any welder you choose, creating more consistent power, better weld puddle, and a cleaner weld.
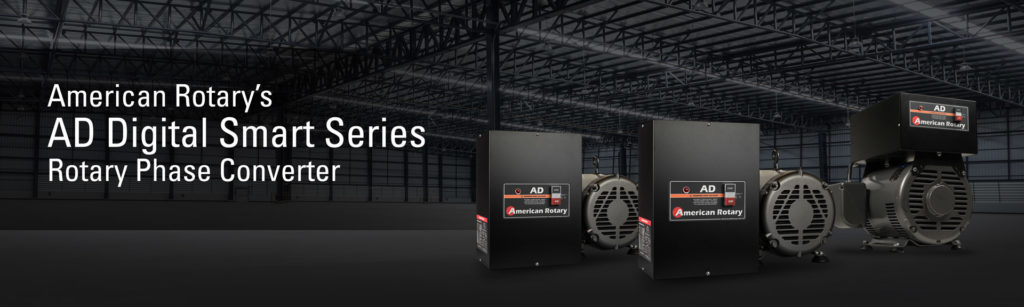
For example, American Rotary’s AD Digital Smart Series Rotary Phase Converter is specifically suited for voltage-sensitive equipment. Learn more about using phase converters for welding here.
Happy welding!