Milling your own lumber is a labor of love. But for a craftsman, a DIY sawmill setup can be a great way to get unique wood material and reduce the total cost along the way. What are your key options, tools, and considerations? Get started with this step-by-step guide.
Let’s say you need some wood for your next woodworking project—a piece of furniture, a bar, a barn, whatever you’re envisioning. You could just go to your local lumber yard and buy the wood you need.
But if you’re a hobbyist, or novice woodworker, the price tag for wood has been making you think twice about that lately, here’s an idea. Have you considered milling your own lumber?
DIY sawmilling isn’t the simplest woodworking challenge for your workshop or garage, but it has many advantages. Given recent lumber price spikes, the potential cost savings over time is a big one. The logs you’re starting with will be free, or at least dirt cheap.
Plus, milling your own lumber can be much more satisfying for a craftsman. It lets you decide the types of cuts, sizes, species and desired grain. You’re not limited by the only-what’s-most-popular selection at the lumber yard. And if you have a big property with a lot of trees that you need to clear? Milling the lumber yourself is faster and cheaper for an enthusiastic hobbyist. You’ll make better use of your own resources in the process.
So, what does it take to start milling your own lumber? Let’s walk through the key considerations at a high level in this step-by-step guide.
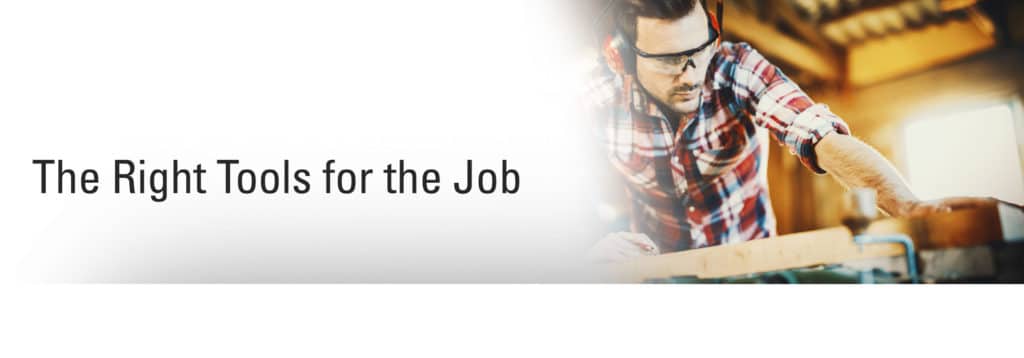
The Right Tools for the Job
First, make sure you have the right space for your sawmill setup.
One of the best things about DIY sawmilling? You can store your wood for drying right by your shop for easy, anytime access. But you do need a good amount of room to do that!
You’ll also need to make sure you have all the components to turn usable logs into timber, including:
Handling equipment – How will you get the logs? How will you load them onto your sawmill? A good skid loader, a heavy-duty trailer, winch, and cant hooks are among the essentials.
Bucking tools – A good chainsaw with both a ripping chain and regular chain is a key tool for trimming your logs to lengths for milling.
Fuel and/or power supply – Make sure you can get the power you need, whether it’s with a gas-powered saw or an electric mill. If the latter, you’ll need to decide whether to use a single-phase or three-phase saw. You’ll also need to ensure you have the power to accommodate it. More on that later.
Protective equipment – Not just guards on the machine, but all due safety measures to protect your eyes, ears and appendages. Milling involves powerful, dangerous machines that warrant caution.
Finishing tools – As I’m sure you’re aware you won’t be able to lay your new flooring from a fresh rough board. You’ll need finishing tools to get useable boards. Some of these tools include a jointer and planer to make smooth unique cuts of wood with good symmetry
The mill itself – That brings us to step 1 below …
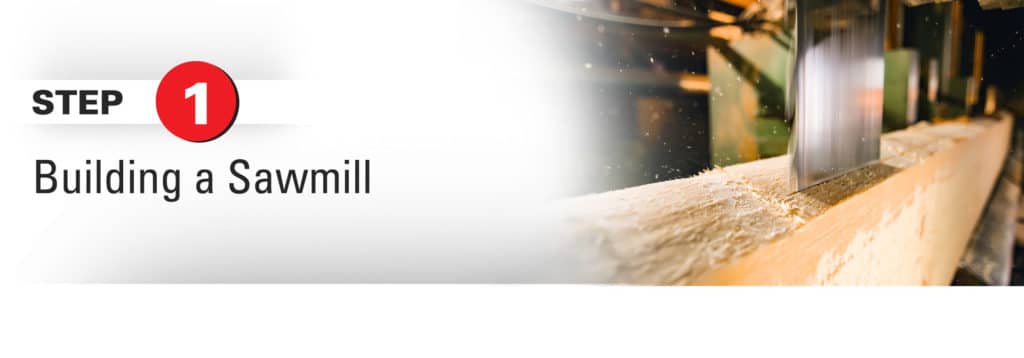
Step 1. Building a Sawmill
Your first consideration in building a sawmill is what type of saw you’re going to use: a chainsaw or a bandsaw. It comes down to how you’ll be using it.
Will you be cutting smaller-diameter logs of softwoods (evergreens such as firs, spruces, and cedars)? A chainsaw mill is a way to go. It’s less costly and more portable.
Or will you be cutting bigger logs and more hardwoods, from deciduous trees such as oak, poplar, cherry, and maple? A bandsaw mill is going to cut more hardwood more efficiently. It’s a thinner blade, which means less kerf (material lost during cutting due to blade thickness).
Here’s some useful information on the chainsaw vs. bandsaw decision.
The second big item for your sawmill is the frame. You can find hundreds of various choices of plans and instructions online. Consider the effort required and the price of raw material when looking at simple structures like this wooden setup. Or more elaborate welded steel systems incorporating hydraulics.
This part of the process is likely to be your most time and labor-intensive.
If you have a bit more budget, you could buy a turnkey, portable sawmill with the frame already included. Be prepared to spend thousands of dollars. But you will save untold time and get to milling your own timber faster!
Besides the mill, you’ll need auxiliary equipment, including bucking, loading, unloading, and holding apparatus to protect the builder.
Bucking is the vital step of cutting logs into usable milling lengths. This task is particularly important for a smaller, home-based sawmill operation. A good bucking setup means you only need the capacity to mill, say, an 8-foot board instead of a 20-footer.
Although you can go basic with bucking and cut your logs on the ground, that requires more advanced skill. It also risks damage to the blade (or you). Instead, you can build a classic sawbuck, an X-shaped sawhorse frame that holds the log up off the ground.
Here are some free plans for simple sawbuck structures.
For handling (loading, unloading and holding), a good winch paired with a ramp is ideal. If you’re more mechanically inclined, you could incorporate a hydraulic handling system like this.
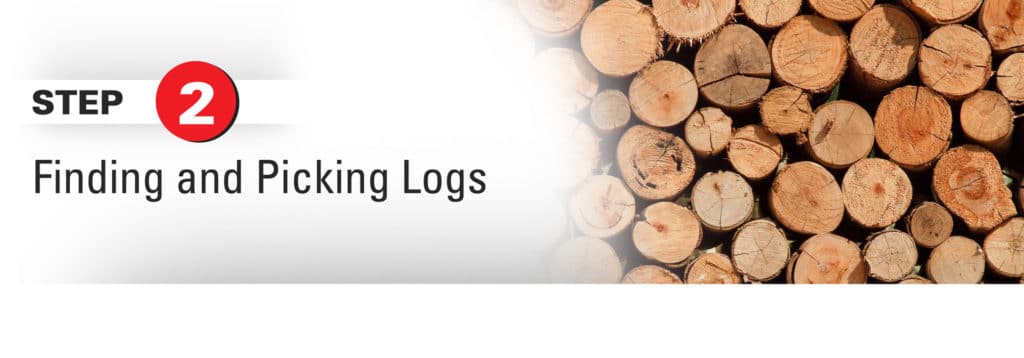
Step 2. Finding and Picking Logs
The real fun begins once you’ve built or bought your sawmill and it’s time to try putting it to use. Where will you find your wood?
If you have a large property with a lot of trees, that’s an obvious place to start looking for useable lumber. Yes, you can mill dead trees, for the most part, just be sure to inspect the log for the important aspects of timber that is healthy and useable. This is especially true if you get to them quickly, which you should be able to if they’re on your property. You’ll need to be on the lookout for rot, and pests in each specific log. You want a healthy log that hasn’t been lying on wet ground for a year to get the best yield.
Even so, a sawmiller or carpenter may find lots of high-grade lumber in dead trees. And even if it turns out to be better suited for firewood, you learn a little more along the way.
Here are more insights on milling dead trees.
Many DIY sawmill operators and hobbyists also find success partnering with tree services and reliable supply sources for the best trees. Connecting with land-clearing construction contractors is another fertile approach. And there’s always Craigslist or Facebook. Post your “wanted” ads, and watch for homeowners trying to get rid of felled trees. Careful: trees from residential areas often contain metal (staples, screws, etc.). This may cause you to take a much more active role in the inspection of the log before you have useable timber. Metal and sawmill cutting don’t mix well!
What species should you look for? That’s up to you. Whether you’re dealing with pine, walnut, ash, or cedar, it helps to be familiar with the type of tree and its attributes.
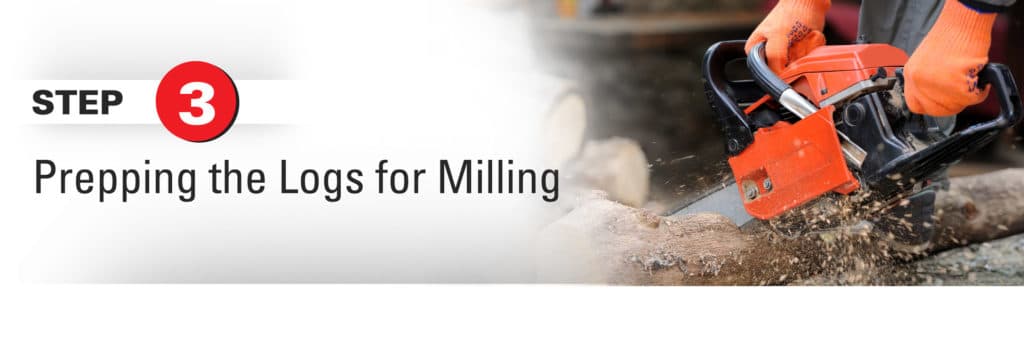
Step 3. Prepping the Logs for Milling
Here’s where that bucking stand you built, as well as your handling equipment, is crucial. It’s time to get that log into a good condition before attempting to make your first cut.
Be sure to cut your sawlogs longer than what you want for the final lumber product. Most experts recommend a 4- to 6-inch trim allowance.
Meanwhile, examine the whole log. Look for any catch points or defects in the bark that could cause problems in handling while on the sawmill. Take a look at the ends to see if you need to remove any wood checks or roughness from initial chainsaw cuts.
It’s also a good time to seal both ends of the logs, which reduces cracks and promotes even drying of the lumber.
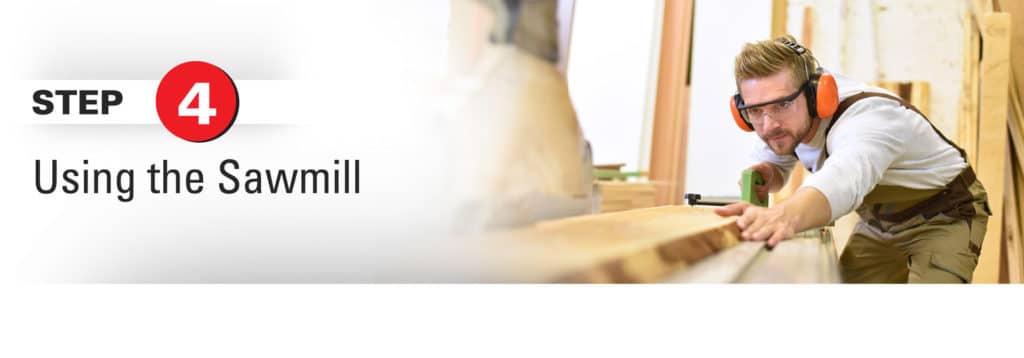
Step 4. Using the Sawmill
With your log prepped, you need to get it into position. Using your winch or hydraulics, get the log onto the frame. Try to position it evenly relative to the saw blade. You may need to account for taper in the log by raising the smaller side so that the pith stays level with the log.
At the same time, you need to decide how you want to orient the log for cutting and getting the best character in the cuts. A good craftsman is always looking for wood with character. So be sure to position your wood to show off knots and other features.
Then clamp down the log tight on the log rests/frame. You don’t want your log rolling due to vibrations from the blade’s power.
You have several options for the types of grain pattern on your rough boards or planks. Your choice will determine whether and when you rotate the log during milling. The three typical grain patterns include:
- Plain – Sawing right through the center of the log all the way down.
- Quarter – Sawing the log into quarters at a radial angle, then plain sawing the quarters from there.
- Rift – Sawing and turning many times to produce more high-quality logs (but also more waste).
The final act of using your sawmill is a long but crucial one: final drying of the harvested timber to prevent warp..
If you plan to air-dry instead of building a kiln, you need good air circulation, a level storage location to build your pile of lumber, and shelter from the elements. After that, the drying process can take up to several months until the moisture content equals the humidity of your local environment.
You may also be willing to build one of the various types of kilns to speed up the process, but this will increase the overall cost of the project, which may not be something that a home hobbyist is willing to do.
But congratulations! You can admire your work in the meantime, and after that, you’ll have good quality wood that you know was made by a real craftsman.
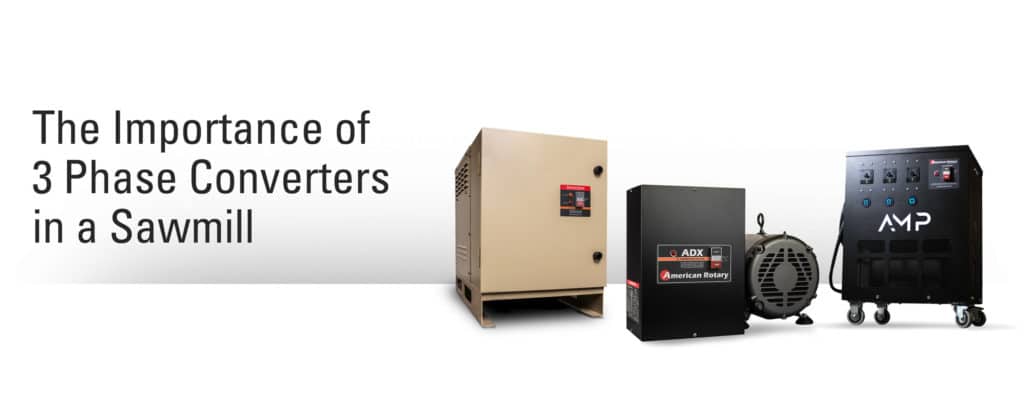
The Importance of 3 Phase Converters in a Sawmill
Don’t forget about power considerations for your awesome new sawmill setup. Gas-powered systems remain common. But if you want to cut the exhaust fumes and reduce noise in a small shop, consider an electric-driven sawmill.
Single-phase electric sawmill blades are available. But sawmilling takes rugged power. For greater workloads and efficiency, a three-phase-powered sawmill might be a better option.
But if you have a shop in a residential or rural area, you may have a single-phase electric utility service. That’s where a three-phase converter comes in handy. It converts your single-phase electricity to smooth three-phase power for your sawmill.
Plus, with proper sizing, you can run your entire shop off a single rotary phase converter. Saws. Dust collectors. Drills. Sanders. You can run it all with the smooth startup and balanced output of American Rotary phase converters.
Learn more about American Rotary phase converters in woodworking.