CNC (computer numerical control) machining makes possible some of the coolest, most complex metal parts you can imagine. It can be a thrill to program a CNC and watch it work its magic by efficiently cutting metal at high precision.
Want in on the action? If you’ve got some manual machining chops and want to step into the more high-tech world of CNC, there’s plenty to learn.
It helps to start with the basics, and we’ve got you covered. Let’s dive in with this guide to CNC machining for beginners.
How a CNC Machine Works
In CNC machining, computer code controls the movement of machine tools and equipment.
The code tells the machine to move in specific directions and at specific speeds. It also gives instructions for cutting and shaping material. Automating these functions enables greater levels of precision, complexity, and production volume compared to manual machining.
All of these are key reasons CNC is big, and getting bigger, in today’s mass manufacturing industries — especially in high-tech markets like aerospace and medical devices.
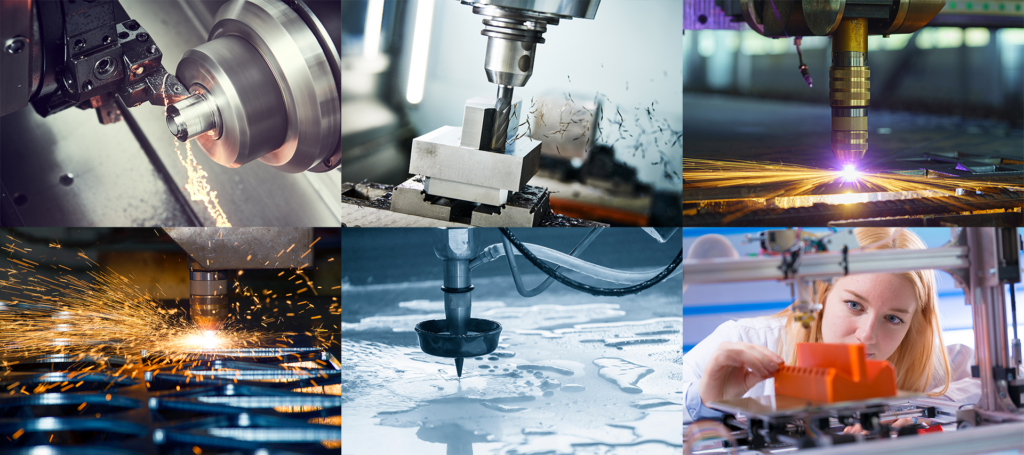
While the two core machining processes are CNC turning and milling, you can find almost any type of machining center with CNC. Popular CNC machines include:
- Lathes — CNC feeds machine tools against a workpiece rotating around a central axis to cut and shape the material. Used to create cylindrical parts like shafts and spindles.
- Milling machines — CNC guides rotary cutters to remove material from a workpiece. Used to create flat and 3D shapes, and to make precise cuts and holes. Check out these 10 easy CNC milling projects, for example.
- Laser cutters — CNC operates a high-powered laser to cut through a variety of materials, including metal, plastic, and wood. Used to create intricate shapes.
- Plasma cutters — CNC guides a high-energy plasma arc to cut through metal and other conductive materials. Used for cutting thick or heavy materials.
- Waterjet cutters — Waterjet cutters use a high-pressure stream of water to cut through a variety of materials, including metal, plastic, and glass. They are often used to create precise and intricate shapes, and to cut materials that would be damaged by other cutting methods.
- 3D printers — An additive rather than subtractive process that uses CNC to build objects layer by layer using a variety of materials, including plastics and metals. Used to create prototypes and small production runs of complex parts.
Get Started With CAD
Like other machining processes, CNC starts with a good print. In this case, the print is a computer-aided design (CAD) drawing.
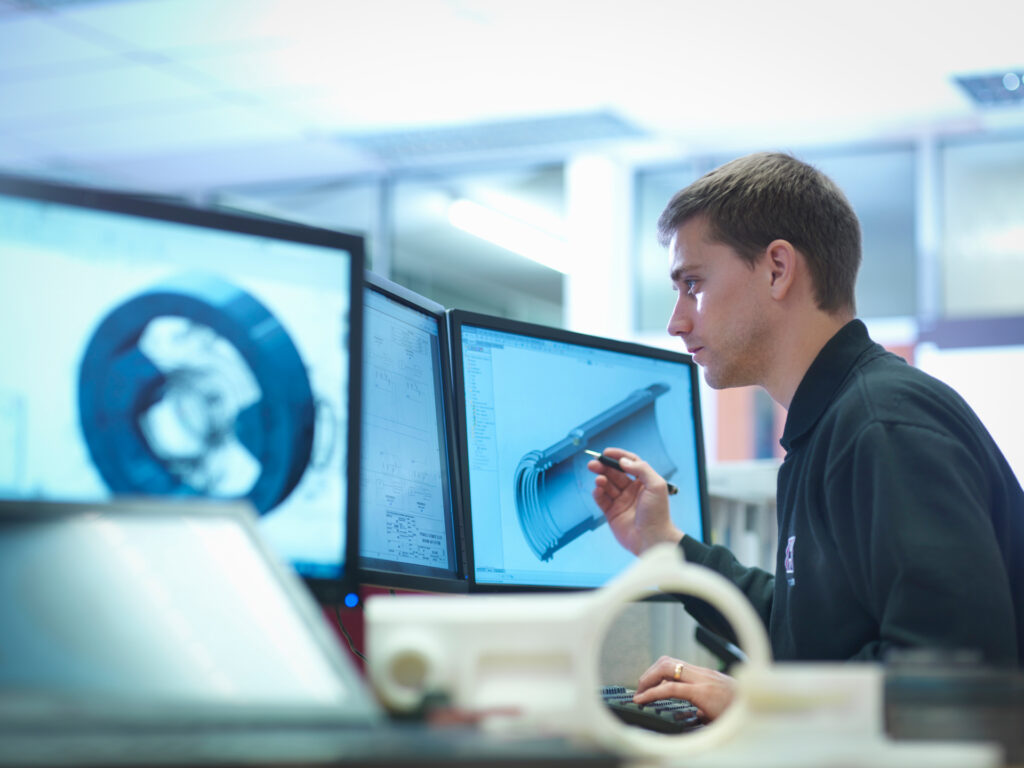
So if you want to get into CNC, you’re going to need to get to know CAD software. Some of the most popular platforms include:
- AutoCAD — A ubiquitous workhorse of architecture, engineering, and manufacturing.
- SolidWorks — 3D CAD specifically designed for mechanical and electrical design, simulation, and product data management.
- Creo (formerly Pro/ENGINEER) — 3D CAD modeling software developed by PTC. It’s used in product design and manufacturing.
- FreeCAD — An open-source 3D CAD modeler, making it accessible to hobbyists and students.
Don’t have any experience with CAD software? There are lots of resources to help you learn.
Online courses on YouTube, Coursera, or even LinkedIn are a good place to start. You could try the official user guides for the software platforms listed above. But some are easier to understand than others.
Then there are books like the classic “For Dummies” series. Or just dive in and start playing around with a trial version of the software.
One way or another, you just need some practice!
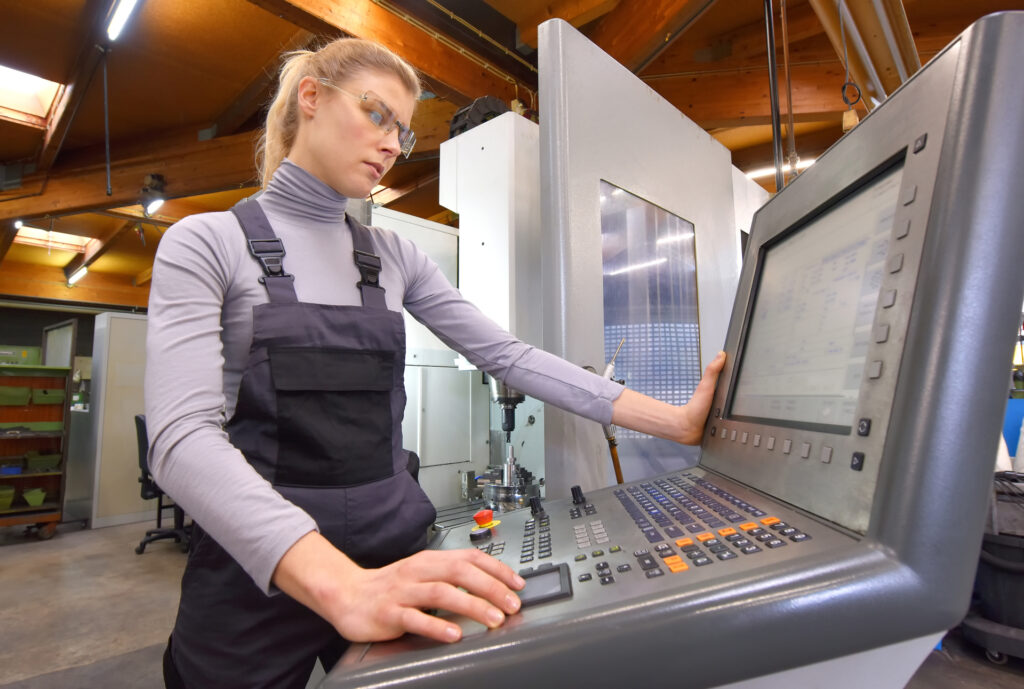
Learn to Program a CNC Machine
OK, so you have your CAD drawing. Now what?
The next step is to convert this design into the actual computer code that will control the movement and functions of the CNC machine.
CNC programming involves two main types of alphanumeric code. There’s G code for the geometry of the machine — where to cut. Then there’s M code for miscellaneous functions, such as changing tools, using coolant, etc.
Today, you don’t necessarily have to master G code or M code programming to succeed with CNC. CAM (computer-aided manufacturing) software converts CAD into appropriate CNC code.
There’s a wide range of CAM software programs optimized for various machining functions. Here are a few examples:
- Mastercam — Widely used, versatile CAM software with modules for milling, turning, wire EDM, and more.
- SolidCAM — An integrated CAM solution for SolidWorks.
- GibbsCAM — GibbsCAM is a comprehensive CAM software with 2D and 3D milling, turning, and multi-task machining capabilities.
- CATIA (Computer-Aided Three-Dimensional Interactive Application) — A comprehensive CAD/CAM/CAE software suite primarily used in aerospace and automotive industries.
- Fusion 360 — A cloud-based CAD/CAM platform for product design, engineering, and manufacturing.
Even with CAM, it still helps to have a good grasp of CNC programming. That’s because certain M codes are specific to different machines and processes.
With this understanding, you can verify the CAM output against manufacturer documentation — potentially avoiding wasted time and material.
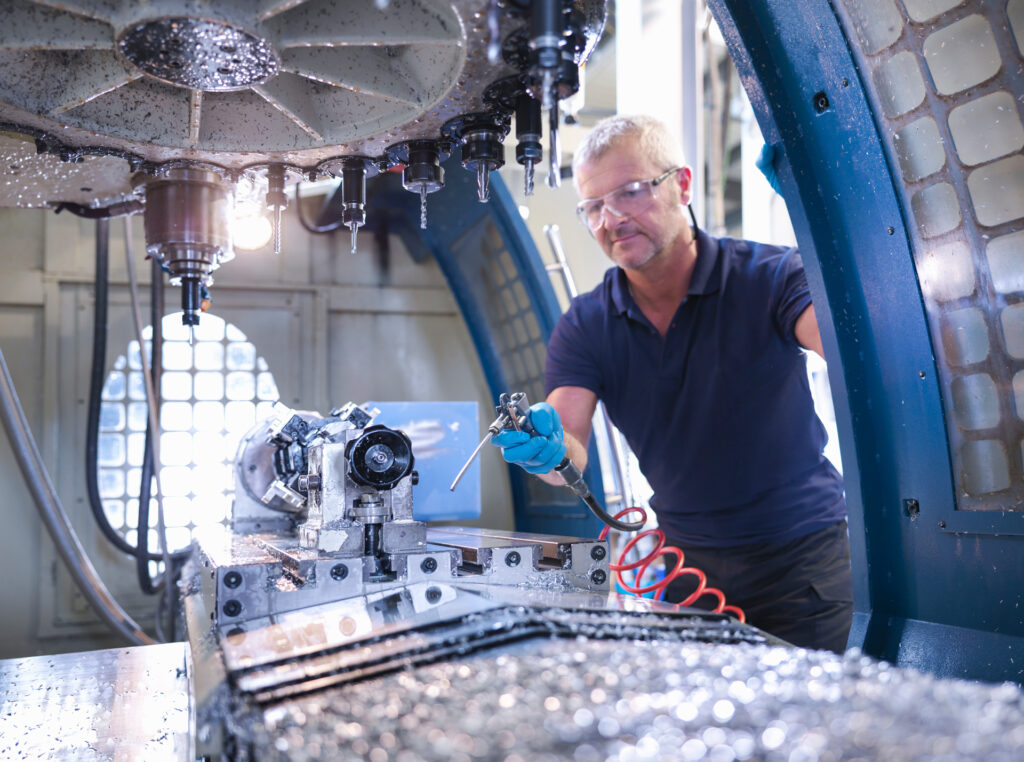
Learn to Set Up a CNC Machine
Once you have your code ready, it’s not quite as simple as pressing a green button to get going.
First, you have to make sure your CNC machine is set up correctly — or you risk costly damage and great frustration.
There’s a fair amount of setup involved before CNC can do its thing. Here are the fundamental steps.
- Clean the machine. Remove any chips, coolant residue, and dust from prior use.
- Load and align your tools. Select the cutting tools for your machining processes. Following manufacturer guidelines, secure the tools in the toolholders or tool changer turret (if your machine has one). Ensure proper calibration and alignment with dial indicators or laser alignment.
- Warm up your machine. Execute the machine’s warm-up procedure. This step gets any thermal expansion out of the way so you don’t run afoul of your tolerances.
- Set your tool length offsets. Measure and set your tool lengths from gage point with a tool presetter or manual measurement. If you’re lucky, your machine has a Tool Length Touch Setter that performs and logs these measurements. Otherwise, you’ll have to do this crucial task manually.
- Install your workpiece. Secure the stock in the CNC machine’s workholding device, such as a vise or chuck. Align the workpiece accurately using reference edges and faces to ensure proper machining.
- Calibrate machine coordinates. Set the position of “workpiece zero” in the work coordinate system (WCS) to align the machine’s reference point for starting your machining processes.
- Load your code. Import your CNC program via USB, local area network, or — if your machine is really old — floppy disk.
- Check your coolant. Make sure it’s in good condition and good supply to protect your equipment, your part, and yourself.
- Do a test run. With all systems going, it’s a good idea to run a cycle with a reduced feed rate and with no workpiece to verify your toolpaths and other parameters,
- Do a test run again. So now you know that the machine isn’t going to run into the fixturing, it’s time to run one more reduced feed cycle with a workpiece loaded to verify your length offsets.
That’s just a quick overview. If you want to go more in-depth, CNC Cookbook is a great resource on machine setup and many other issues.
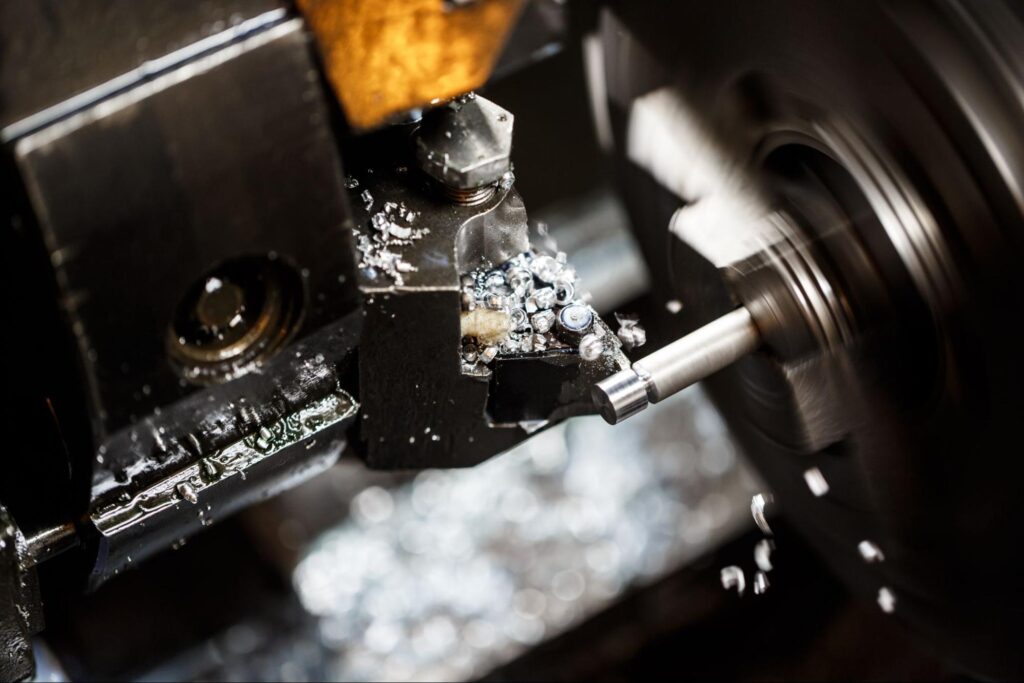
What to Look Out For When Using a CNC Machine
One trick with an automated system like CNC is that once it starts running, it’s out of your hands. It’s literally behind closed doors.
So there isn’t much you can do while it’s cutting other than to bring things to a complete stop.
But you still should stay alert with your eyes, ears, and even your nose. Do it for your own safety, as well as for future success in your CNC machining processes.
Watch your cutting tools through the glass. Listen for unusual sounds or loud bangs. Keep an eye on your coolant flow. Monitor temperatures on your control screen. And, of course, if you see smoke or smell something burning, shut things down, stat!
After you run each workpiece, do a visual inspection and look for imperfections. They could be signs of improper setup or a problem with operation.
Understand Tooling and Power Requirements
If you make a significant investment in a CNC machine, don’t mess it up with what’s arguably the most important factor in your success: your tooling.
It pays to use high-quality tooling to maximize accuracy, precision, and surface finish. You also reduce the risk of tool breakage and machine damage.
Finally, here’s one more — often overlooked — key to getting great CNC results.
You need a stable and consistent power supply for your machine. You’ll almost always need 3-phase power instead of the common single-phase electric utility service.
But you don’t have to spend thousands getting 3-phase brought to your workshop. For a lot less money, you can get a rotary phase converter to do the conversion for you.
USA-made American Rotary phase converters for machining provide reliable, balanced power for precision metalworking. Any of our units can be sized to power just about everything in your hobby machine shop, including both single- and 3-phase equipment at the same time.
Here’s more about choosing the right phase converter. Or feel free to contact us today for help with sizing or any other questions. CNC is an exciting discipline, and we’d love to help you get started!