Machining is the precise process of removing metal or other materials to make a wide variety of useful tools and parts. Machinists in machine shops use mills, lathes, and other equipment to cut away and shape workpieces to precise specifications. Read on to explore the basics of this key manufacturing discipline.
Think of an object made of metal. A pocket knife. Automotive or bike parts—even aerospace parts. Any kind of bolt or screw.
No matter what the part is, machining almost certainly played a role in the manufacturing process. It’s a technical process that takes study and practice to learn. If you’re interested in picking up machining as a hobby or career, we’re here for you with this overview.
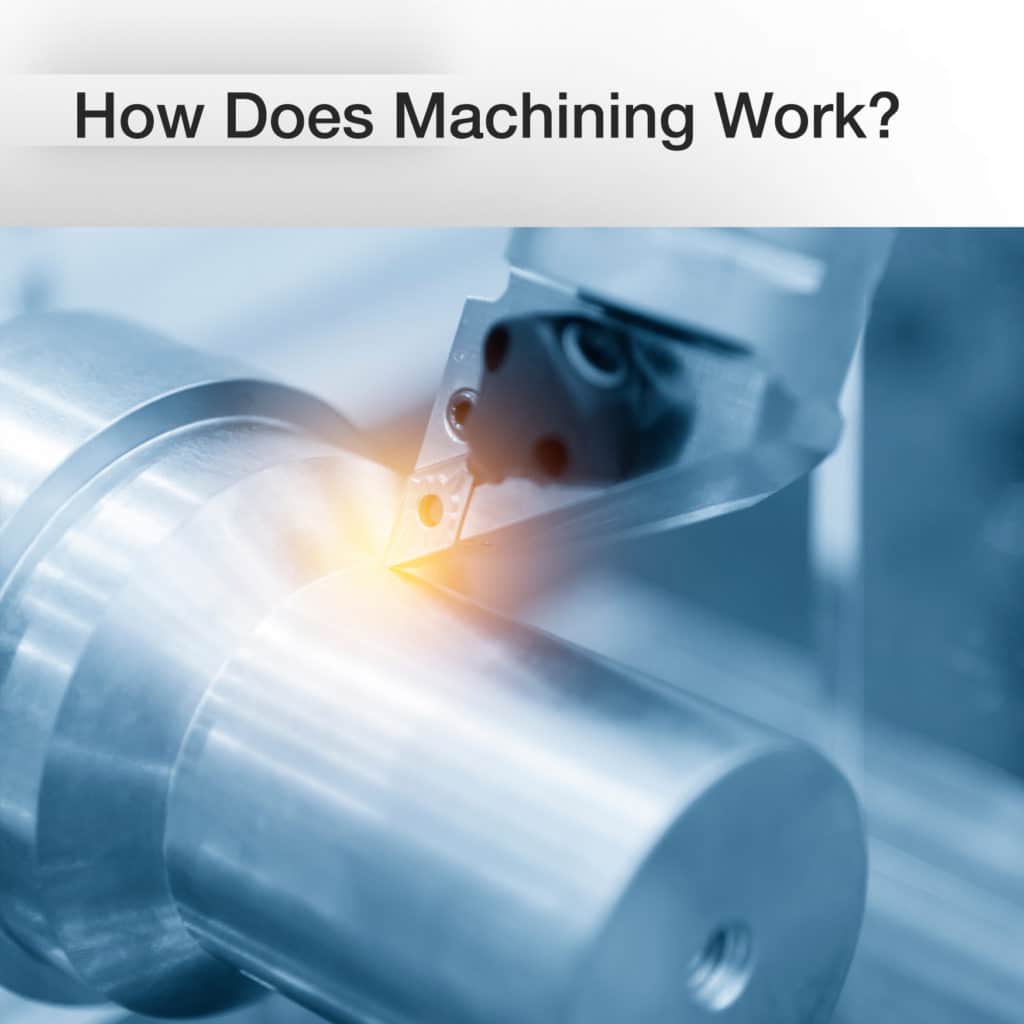
How Does Machining Work?
From engines to appliances to all kinds of mechanical products, parts made via machining are everywhere in our daily lives.
Machining processes involve precisely cutting material into a desired shape to create parts that meet specific functional needs. These common processes can be performed manually or programmed on a computer—as in CNC (computer numerical control) machining.
CNC machining is a form of automation that enables a repeatable sequence of multiple, precise machining processes, making high-quality workpieces in far less time than they take to make manually.
The major downside to CNC machining is that you need some serious dough to purchase these machines. Even then, you will likely need to machine your initial fixtures on a manual machine.
The price for your two basic pieces of CNC equipment—a CNC milling machine and a CNC lathe—can be upwards of a hundred thousand dollars for two high-quality machines and all the tooling required to run them. Meanwhile, you can get two manual machines for just a few grand.
However, if you have one check out this list of CNC milling projects, and this guide to cnc machining for beginners to learn and advance your skills.
Keep in mind that all the machining processes are a form of subtractive manufacturing, meaning they work by removing material. Think of it as precision sculpting—uncovering the part inside the material.
On the other hand, additive manufacturing techniques also are gaining popularity. This approach involves creating a part layer by layer from a digital model. Additive machining is basically a type of 3D printing, so we’ll continue to focus here on the traditional subtractive machining processes.
What Materials Can be Machined?
Machining primarily works on metal materials, but machinists occasionally work with wood, ceramics, and certain hard plastics.
For example, polyoxymethylene, often known by the brand name Delrin®, is suitable for various machining processes due to its stiffness and dimensional stability.
As for metals, machine shops mainly work with many types of stainless steels and iron. Aluminum is also commonly machined but can be more challenging to work with because it’s not as hard and has a low melting point (read this list of tips for machining aluminum for more info). The most workable metal materials fall in the midrange of hardness and have a high melting point.
Common Machining Processes
Machining is a broad term that refers to several types of machining operations, each of which may use different sets of tools and attachments. Below we’ve listed some of the most basic types of operations and how to answer the question of when to use a milling machine vs. a lathe. But there many more ranging from the 3 core machining operations in turning, milling, and drilling, to less common and more specialized types like EDM.
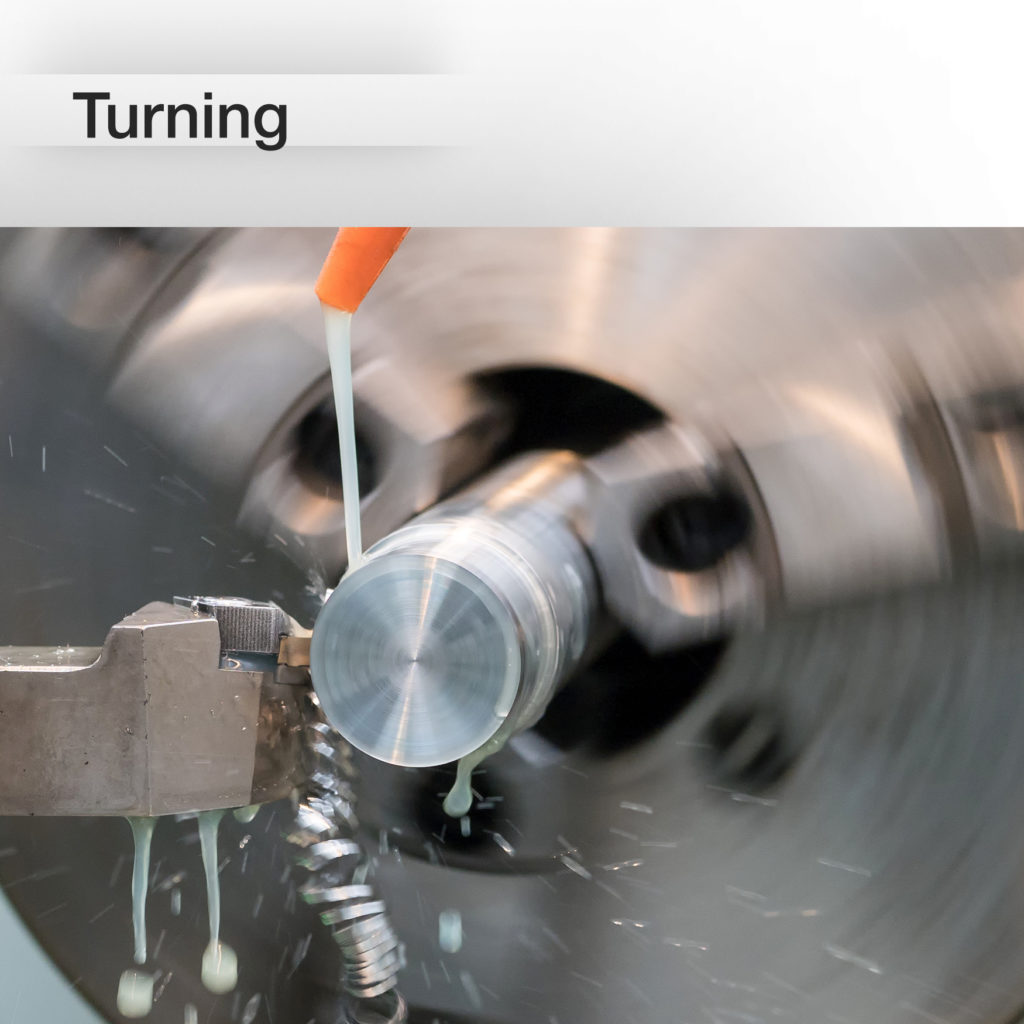
Turning
Turning means rotating a workpiece to move the material against the cutting edge of a tool to shape it into the form you want.
A horizontal lathe is probably the most basic piece of machining technology and the most popular machine for turning. Cutting tools you might use on the rotating workpiece include a facer to remove material from an end; or a grooving tool to cut grooves into the piece.
Take a look at our list of cool metal lathe projects for a bunch of fun things to do with your lathe.
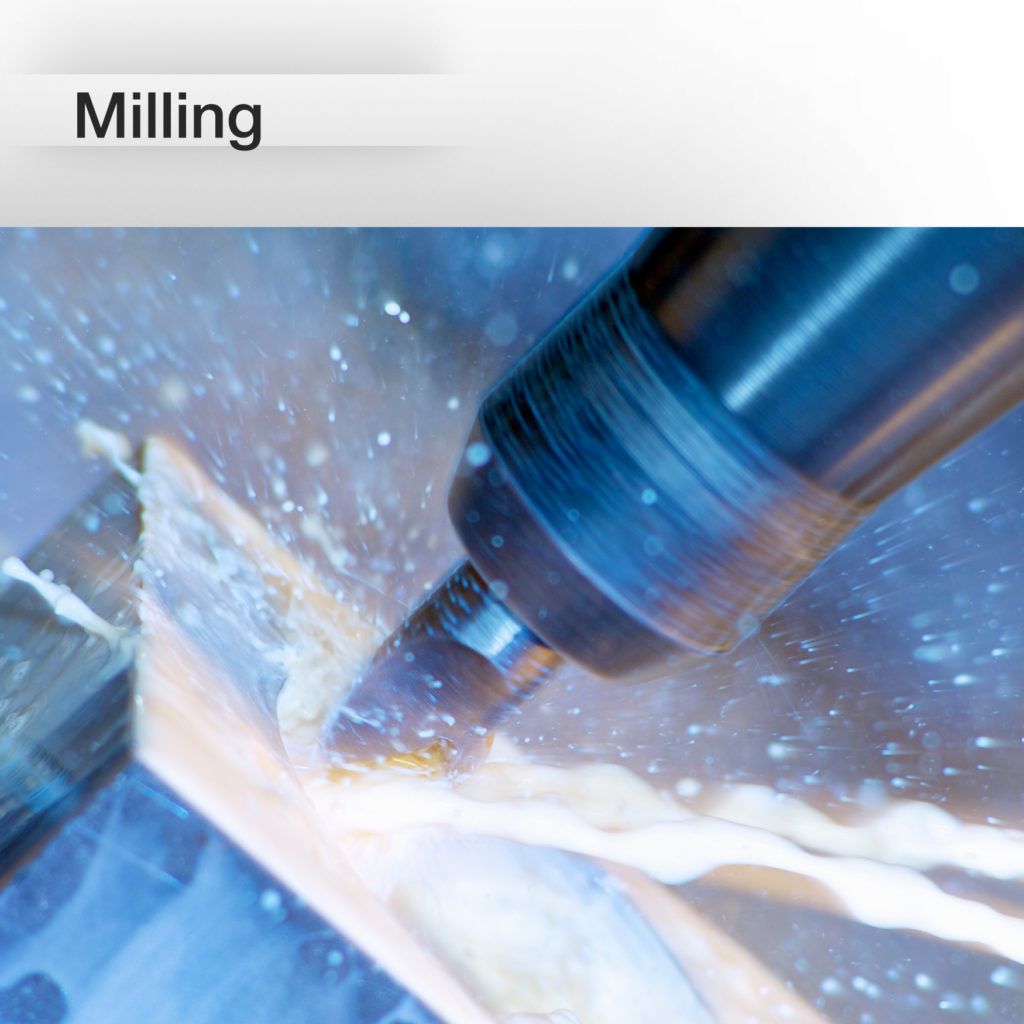
Milling
In milling, instead of the workpiece spinning, you bring a rotating cutting tool up against your workpiece to make your cuts.
The famous Bridgeport style or knee mill is the most common piece of equipment for milling. With a wide variety of cutting tools, milling is a versatile process that enables the cutting of flat or irregular surfaces and drilling or boring holes and slots on your workpiece to create any type of part geometry your project calls for.
Even a beginner can tackle plenty of awesome milling machine projects—everything from cost-saving attachments for your machining tools to fun projects like metal dice.
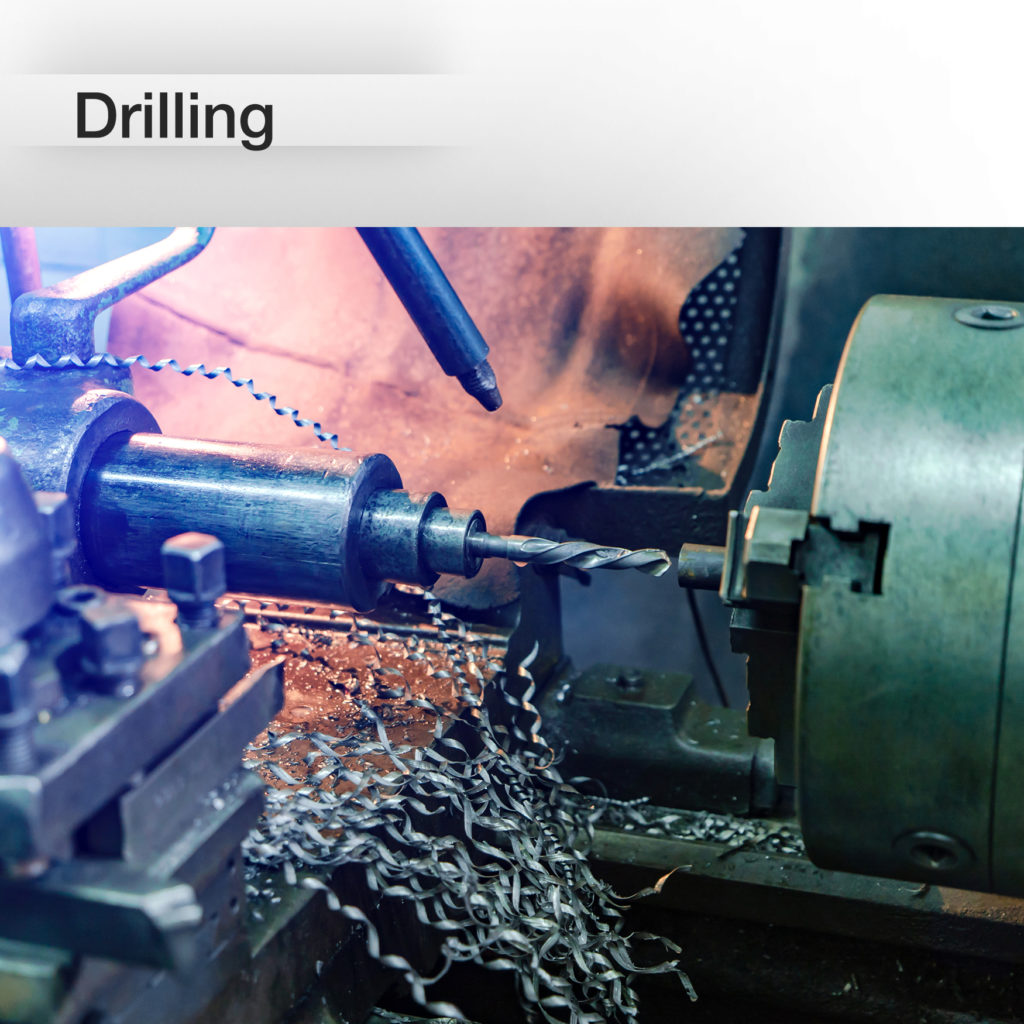
Drilling
Drilling is the process of creating a round hole by driving a rotating drill bit into your workpiece. While most people associate a drill press with this task, that machine just isn’t precise enough for machining.
For this reason, machinists almost always drill on a milling machine using the X and Y axes for precise placement of the hole and the Z axis for drilling the hole itself.
With the right drilling tools, you can also drill on a lathe. Depending on the desired location of the hole, machinists will sometimes use a lathe instead of a mill.
For example, a center hole on a turned workpiece would most likely be made on a lathe.
In addition to basic drilling of a hole, you might also be doing related drilling processes such as:
- Boring: Expanding an existing hole to precise measurements
- Reaming: Smoothing or evening out the walls of a hole
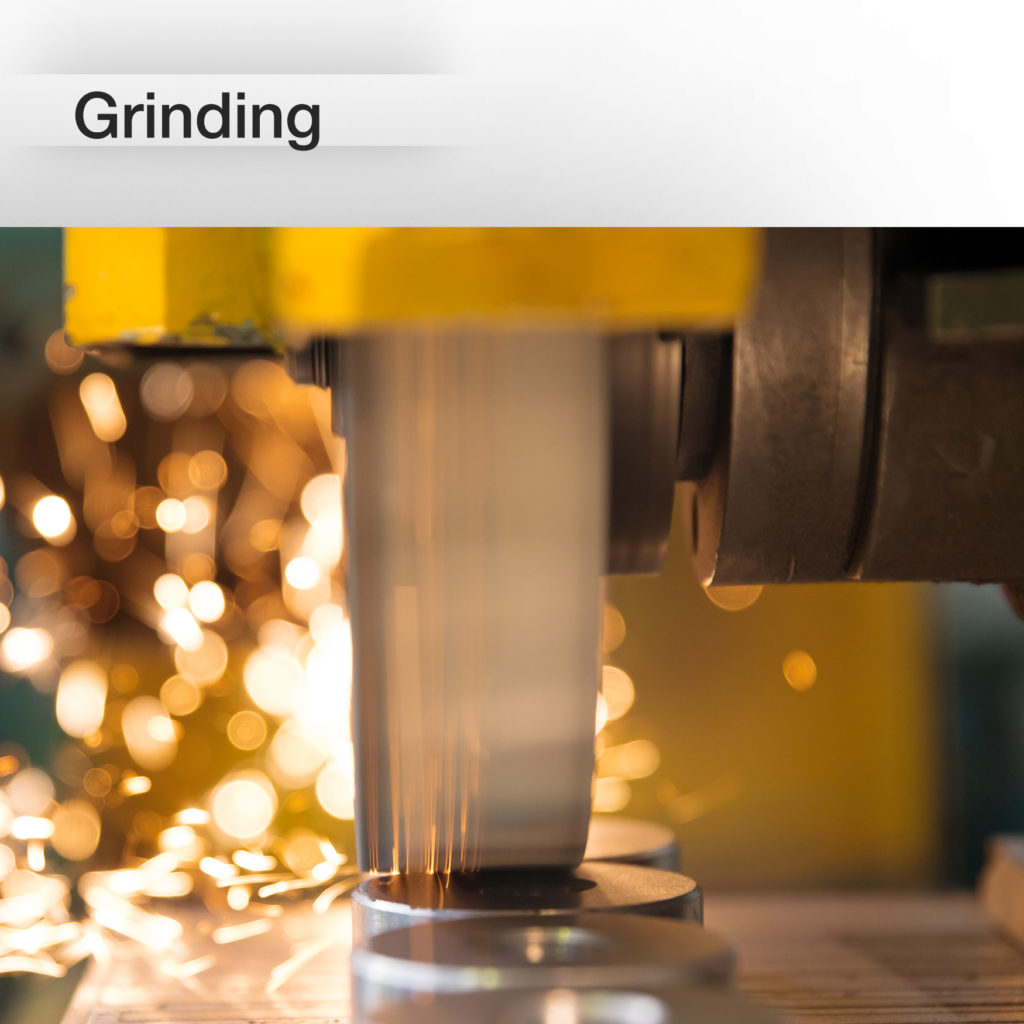
Grinding
Grinding involves smoothing the surface of a part or sizing down to a very tight tolerance for an exact fit.
There are many different types of grinders, but most aren’t suited for a machinist’s work.
The benchtop grinders and pedestal grinders that you might find in a big box store are generally for rough work. They’re good for sharpening tools or removing imperfections from raw material before putting the stock into a machine.
The problem is that these tools aren’t precise enough for precision machining, so they use either a machinist’s surface grinder or a cylindrical grinder on a workpiece to get a perfect finish.
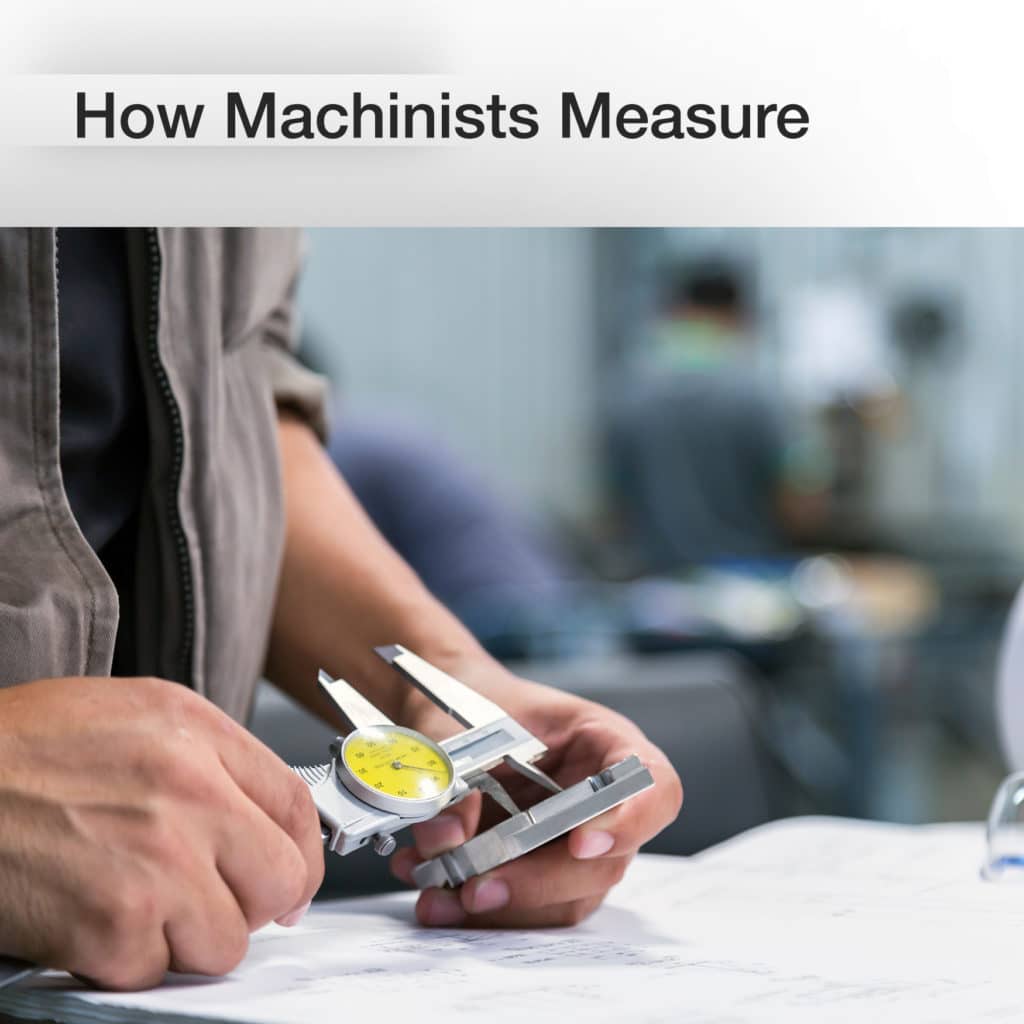
How Machinists Measure
Machining requires a high level of precision. A tenth of an inch, even a hundredth of an inch, isn’t exact enough.
That’s why machinists base all their measurements on a thousandth of an inch. So, some terms to keep in mind include:
- Thou – Nickname for the base thousandth-inch measurement
- Tenth – Not a tenth of an inch, but 1/10 of 1/1000 inch – or 0.0001 inch
- Ten thou – 10 thousandths of an inch, or 0.010 inch
- Hundred thou – 100 thousandths of an inch, or 0.100 inch
Aside from the unique terminology, machinists also use distinctive measuring tools, such as calipers, which act like a swiss army knife for measuring, allowing multiple ways to measure in one tool. They do have a major drawback, though, and that’s accuracy. Most quality sets of calipers are accurate down to the thousandths and have a deviation of ±.001.
But what do you do when you need to be more precise than that?
While it’s more difficult to use, far more specific, and slower, a micrometer is the tool a machinist would choose since most measure down to the .0001 of an inch and have a deviation of ±.0001.
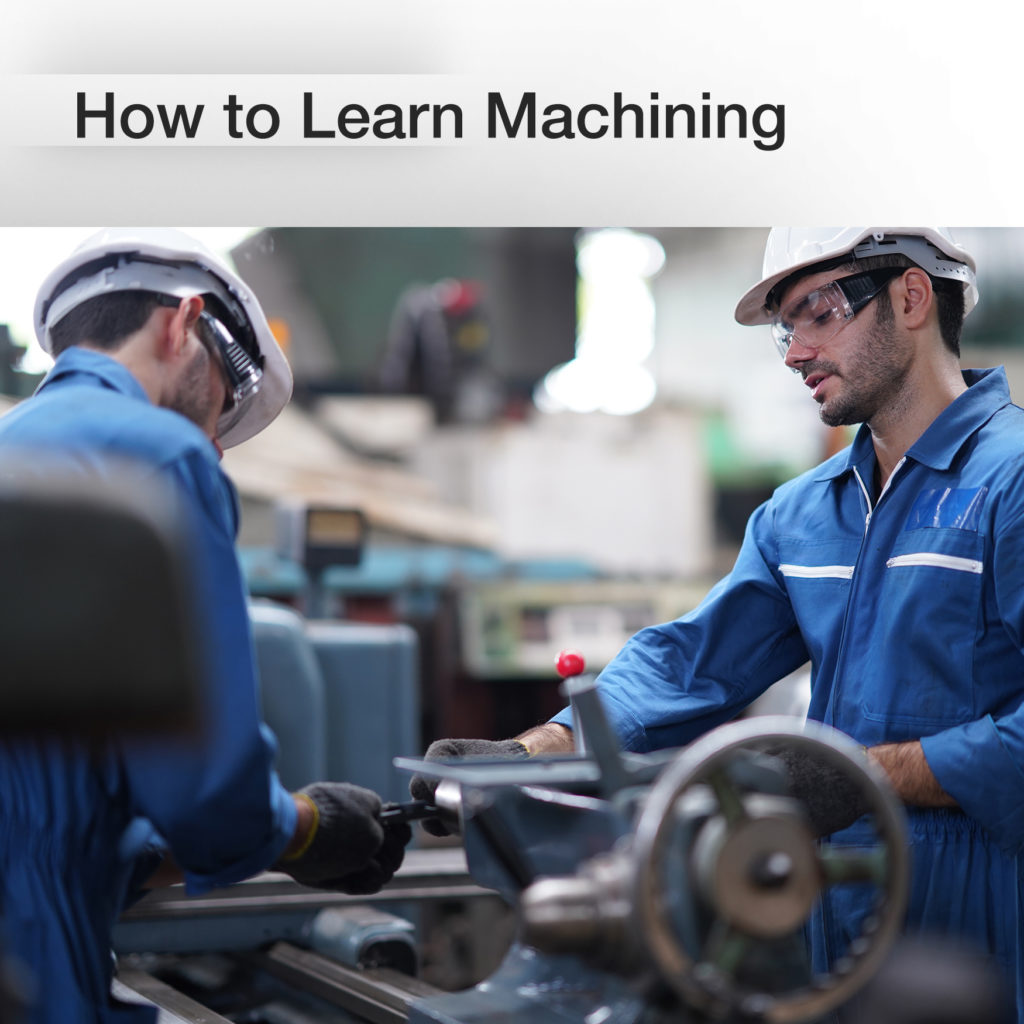
How to Learn Machining
Machining is an advanced technical skill best learned by practicing under the watchful instruction of an expert.
If you want to get into machining as a career, you may be able to find an entry-level spot at a machine shop where you can train on the job. Otherwise, many community colleges and technical schools offer machining courses led by experienced pros.
If you’re interested in machining as a hobby, it helps to connect with someone who already knows what they’re doing and give you the important beginner machinist tips. You can get a primer on all kinds of machining techniques online, but nothing beats learning by doing with the help of a seasoned machinist. Or you can enroll in a continuing education class.
However you choose to get there, remember that machining skills take lots of practice. Be patient with yourself and enjoy the learning process!
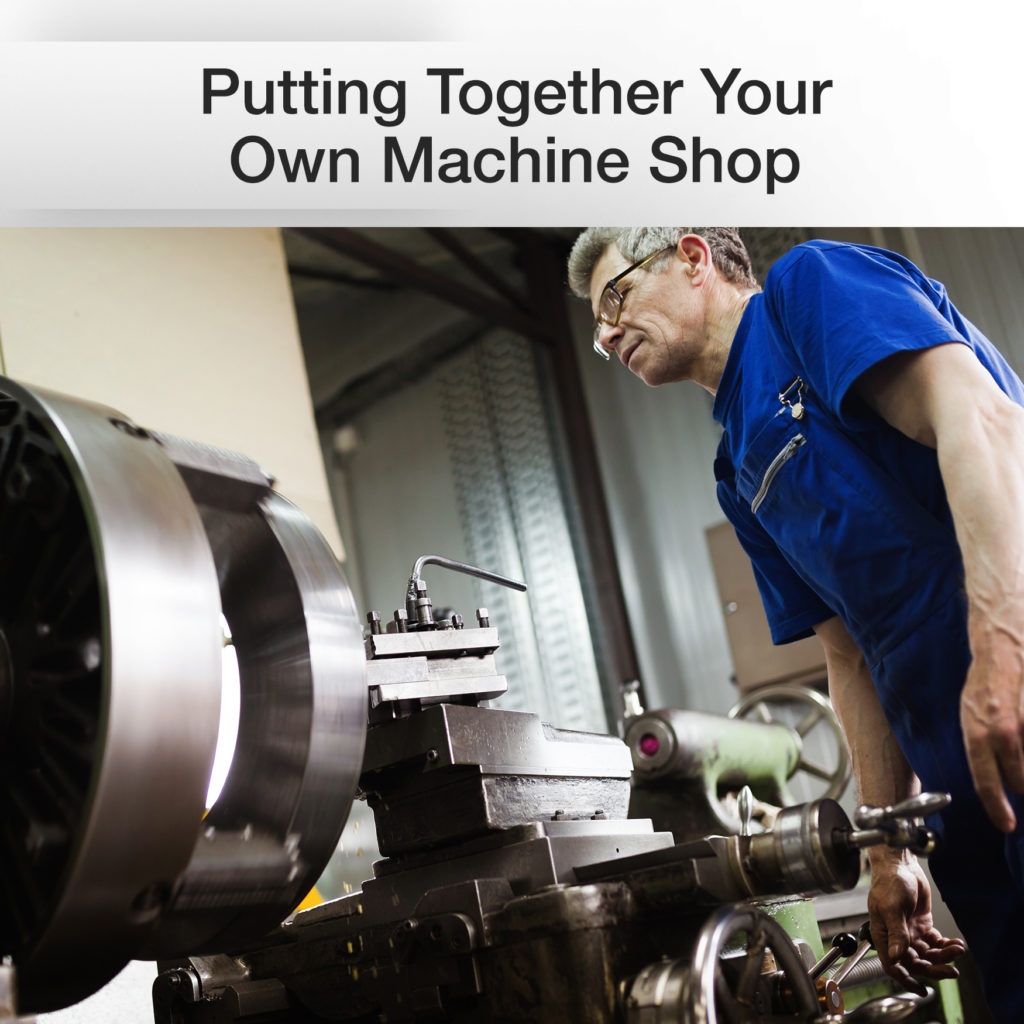
Putting Together Your Own Machine Shop
We won’t kid you: Machining equipment is a big investment.
Unless you just got a big inheritance or won the lottery, you might not have the dough sitting around to drop on a whole shop full of new machines.
So where should you start?
The big two: a lathe and a mill.
If you’re interested in starting a machine shop, take your time and do your research because if you make a good call on these two versatile machines, you’ll be set up to do nearly any machining project you can imagine.
Later, as you find more funds (or sell some of your machining services?), you can add on other machines like a grinder or broach for more specialized processes.
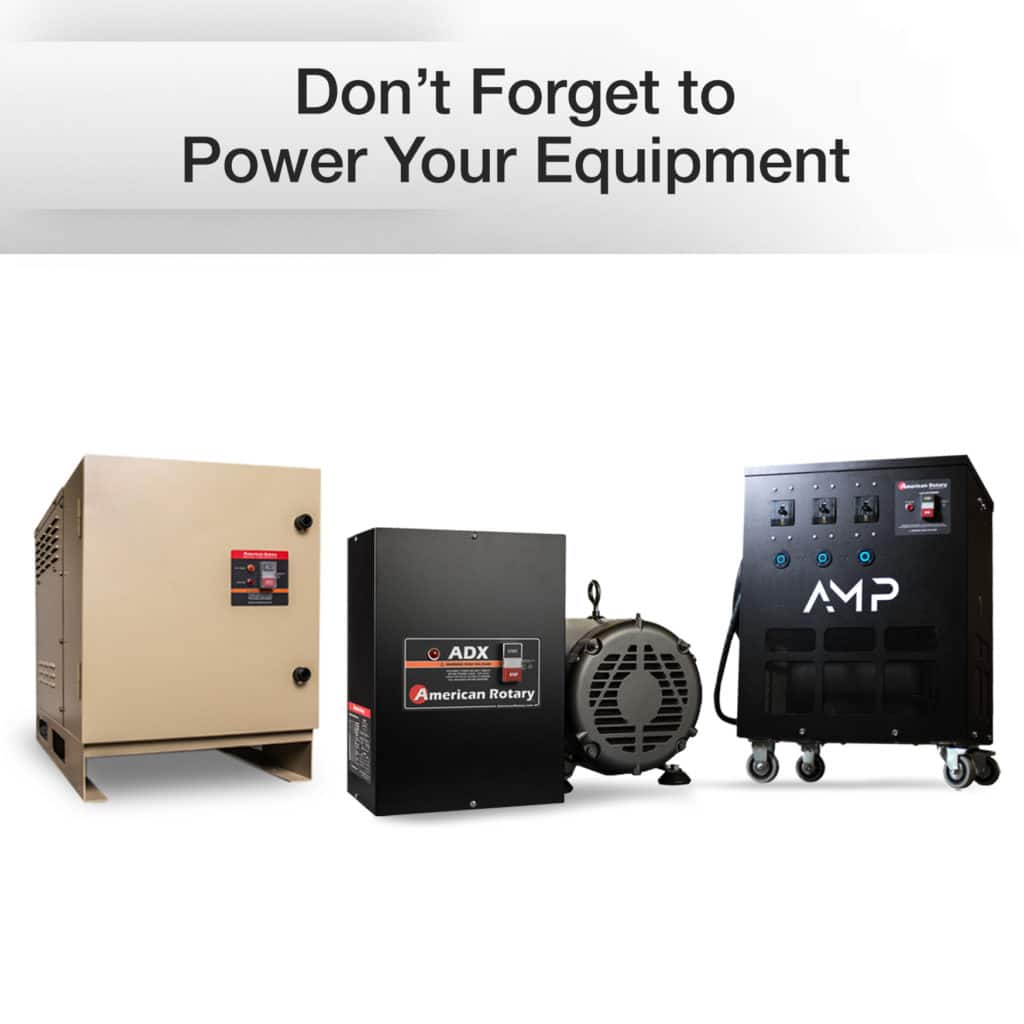
Don’t Forget to Power Your Equipment
You may know that more powerful equipment makes cutting through metal and other tough stuff much easier. But did you know that, for higher-horsepower equipment, 3-phase power provides smoother operation and higher efficiency?
That’s why, if you have a choice between single-phase and 3-phase powered machining equipment, the 3-phase is likely worth it.
You’ll enable a better surface finish, expand the life of expensive machine tools, and create less scrap.
The challenge is that most home shops don’t have 3-phase electric service. In that case, a rotary three-phase converter may be a great solution.
Rotary phase converters—including USA-made American Rotary phase converters—can convert your single-phase electricity to provide the balanced 3-phase power your shop needs. You can power everything in your shop, including both single-phase and 3-phase equipment, with one properly sized rotary phase converter.
If you need help getting the right size converter, feel free to contact us. Once you learn your machining fundamentals and have some starter equipment up and running, you’ll be good to go on your machining journey!